Unveiling the Intriguing World of Common Metal Alloys: A Detailed Analysis
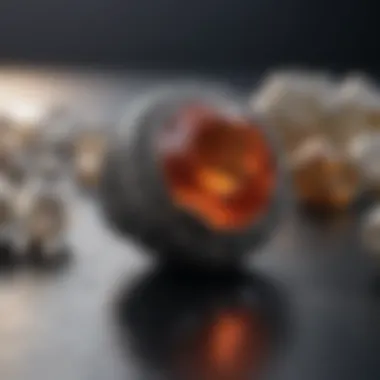
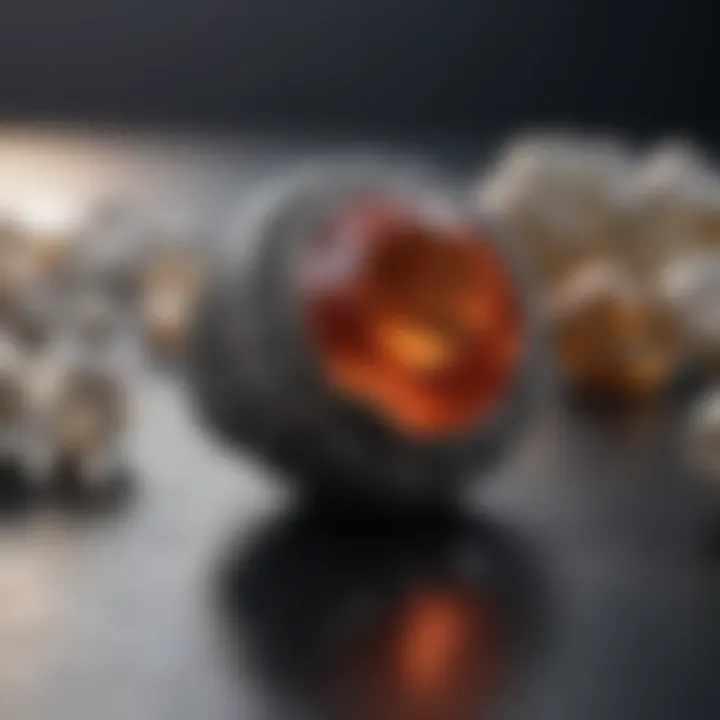
Overview of Common Metal Alloys
Common metal alloys have played an integral role in various industries, exhibiting a wide range of chemical compositions, physical properties, and practical applications. From the ubiquitous stainless steel utilized in everyday products to the specialized superalloys engineered for high-performance aircraft components, the realm of metal alloys is as diverse as it is fascinating.
Composition and Properties of Metal Alloys
Metal alloys derive their unique properties from a combination of base metals and alloying elements. Understanding the composition of these alloys is crucial in predicting their behavior under different conditions. Factors such as hardness, strength, corrosion resistance, and conductivity vary based on the alloy's composition, making each alloy suitable for specific applications.
Discussing the process of determining the ideal combination of metals and elements to achieve desired properties will shed light on the complexity and precision involved in alloy development.
Industrial Applications of Metal Alloys
The industrial significance of metal alloys cannot be overstated, as they form the backbone of modern manufacturing and construction sectors. By exploring their applications across various industries, from automotive and aerospace to electronics and architecture, we gain insight into how these versatile materials drive innovation and shape the world around us.
Diving deep into the specific uses of common metal alloys in different sectors will showcase their adaptability, strength, and durability, highlighting their indispensable role in shaping our modern lifestyle and technological advancements.
Introduction
In this detailed guide on exploring common metal alloys, we delve into the intricate world of metallic compounds that play a pivotal role in various industries. Metal alloys are essential in modern manufacturing processes and are known for their enhanced properties compared to pure metals. By combining different metals, engineers can create materials with specific characteristics tailored to meet diverse industrial requirements and applications. This comprehensive exploration will shed light on the composition, properties, and applications of a wide range of metal alloys, from everyday stainless steel to specialized superalloys.
Understanding Metal Alloys
Definition of Alloys
Metal alloys refer to materials composed of two or more metallic elements, where the resulting material exhibits unique properties different from its individual components. The blend of metals in an alloy aims to enhance specific traits such as strength, durability, or corrosion resistance, making alloys a preferred choice in various industries. The ability to customize alloy compositions allows for a wide range of mechanical and chemical properties to be achieved, offering versatility in material selection for specific applications.
Significance in Material Science
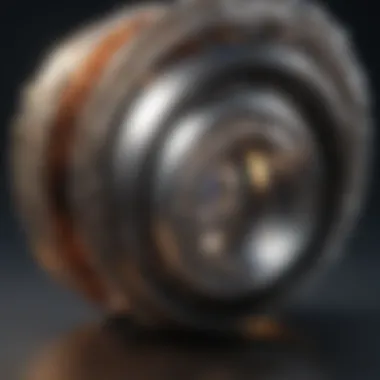
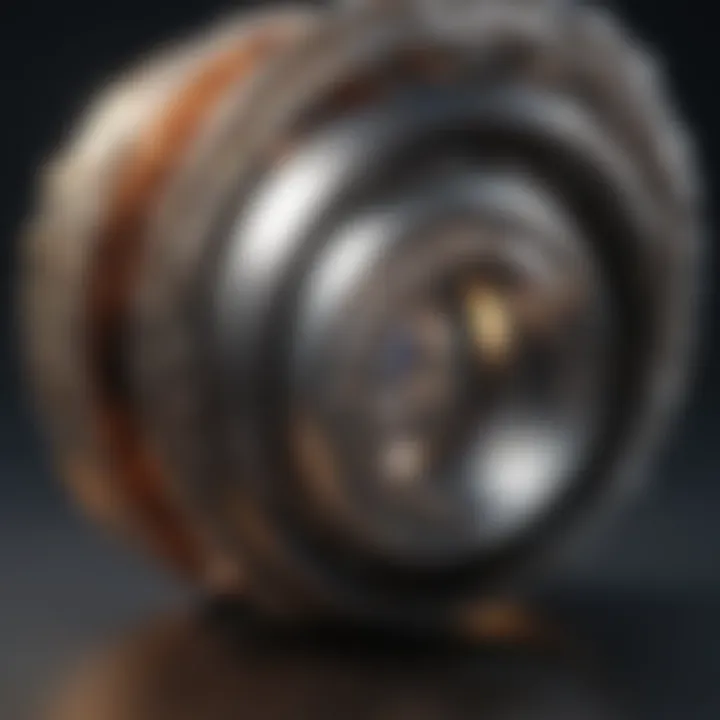
The significance of alloys in material science lies in their transformative impact on technological advancements and industrial processes. These compounds enable the development of materials with superior properties compared to pure metals, expanding the possibilities for innovation and engineering solutions. Alloys play a crucial role in optimizing material performance, leading to the creation of high-performance components that drive progress across sectors such as aerospace, automotive, and electronics.
Classification of Metal Alloys
Ferrous Alloys
Ferrous alloys, which primarily contain iron as the base metal, are renowned for their strength and magnetic properties. These alloys find extensive use in structural applications, machinery, and transportation due to their robust nature and formability. The inclusion of elements such as carbon and nickel in ferrous alloys imparts specific qualities like increased hardness and rust resistance, making them valuable in challenging environments.
Non-Ferrous Alloys
Non-ferrous alloys exclude iron as the primary constituent and encompass a broad range of metals like aluminum, copper, and titanium. These alloys are valued for their lightweight nature, corrosion resistance, and conductivity, offering key advantages in sectors requiring non-magnetic and highly conductive materials. Non-ferrous alloys have diverse applications in industries such as construction, electrical engineering, and marine engineering.
High Strength Alloys
High strength alloys are engineered to withstand extreme conditions while maintaining their structural integrity and performance. These alloys are developed through specialized heat treatment processes and alloying techniques to enhance properties like tensile strength, toughness, and heat resistance. With applications in critical settings such as aerospace, defense, and energy production, high strength alloys are at the forefront of technological innovation and safety standards.
Common Types of Metal Alloys
In this comprehensive guide on metal alloys, the section focusing on common types of metal alloys holds significant importance. Metal alloys play a crucial role in various industries due to their unique properties and applications. Understanding the composition, properties, and industrial uses of common metal alloys offers valuable insights into the diverse world of metallurgy.
Stainless Steel Alloys
Composition and Properties
Diving into the composition and properties of stainless steel alloys reveals a fascinating aspect of these materials. Stainless steel is renowned for its corrosion resistance, making it a popular choice in diverse applications. The unique combination of iron, carbon, and chromium leads to the formation of a protective oxide layer, enhancing durability and longevity. This corrosion resistance property sets stainless steel apart from other alloys and contributes to its widespread use in various industries.
Stainless steel alloys also exhibit exceptional strength and heat resistance, adding to their versatility in industrial applications. The ability to maintain structural integrity under high temperatures makes stainless steel an ideal choice for demanding environments. However, the high cost of production and potential susceptibility to pitting corrosion are notable considerations when utilizing stainless steel alloys.
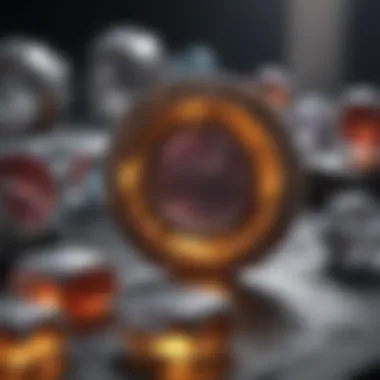
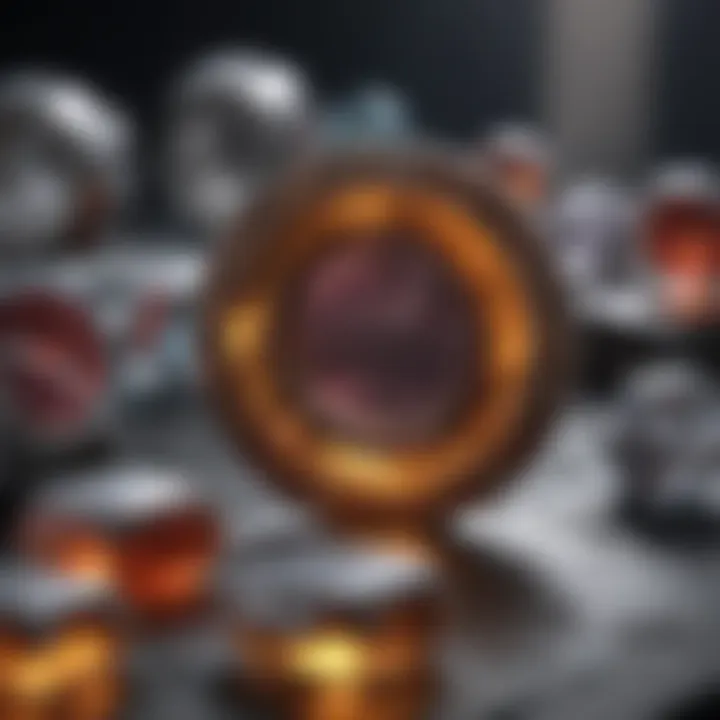
Applications in Industry
The industrial applications of stainless steel alloys are vast and significant. From manufacturing to construction, stainless steel finds extensive use in various sectors. Its resistance to corrosion makes it a preferred material for structural components in buildings, bridges, and infrastructure projects. Additionally, the hygienic nature of stainless steel makes it a top choice for medical equipment, food processing machinery, and pharmaceutical applications.
In the automotive and aerospace industries, stainless steel alloys play a crucial role due to their strength, durability, and aesthetic appeal. Components such as exhaust systems, aircraft fuselages, and architectural features benefit from the corrosion resistance and low maintenance requirements of stainless steel. Despite the initial higher cost of stainless steel, its long-term benefits and environmental sustainability make it a valuable investment in industrial operations.
Specialized Metal Alloys
Specialized metal alloys play a crucial role in forging innovative solutions across various industries, making them a focal point in this comprehensive guide. These alloys encompass a range of unique compositions that offer distinct advantages, setting them apart from conventional metal mixes. Their significance lies in their tailored properties that cater to specific applications, ensuring optimal performance and longevity. By delving into specialized metal alloys, we unearth a realm of advanced materials that push the boundaries of traditional alloy functionality.
Superalloys
High-Temperature Applications
The realm of high-temperature applications within superalloys showcases their ability to withstand extreme thermal conditions, making them indispensable in demanding environments. The key characteristic of these superalloys is their exceptional heat resistance, ensuring structural integrity and performance under intense heat stress. This exceptional heat resilience makes them a popular choice in manufacturing components for aerospace, gas turbines, and nuclear reactors. Despite this advantage, the stringent manufacturing processes and high costs associated with superalloys are noteworthy considerations.
Gas Turbines and Nuclear Reactors
Superalloys, particularly in the context of gas turbines and nuclear reactors, demonstrate their unparalleled strength and durability. Their key characteristic lies in their ability to maintain structural stability and resist deformation at elevated temperatures, a critical feature for ensuring operational efficiency and safety. These superalloys are a beneficial choice due to their ability to withstand corrosive environments and high mechanical stresses, providing longevity and reliability in challenging applications. However, their high cost and intricate machinability are essential factors to consider when leveraging their exceptional properties.
Shape Memory Alloys
Unique Deformation Characteristics
Shape memory alloys present an intriguing aspect with their unique deformation characteristics, offering a blend of elasticity and shape memory that sets them apart from conventional alloys. The key characteristic of these alloys is their ability to return to a predefined shape upon the removal of a mechanical load, making them ideal for applications requiring repeated bending or actuation. This distinctive feature positions shape memory alloys as a popular choice in biomedical and robotics applications, where precision and adaptability are paramount. However, the potential brittleness and limited fatigue life of these alloys warrant careful consideration in their utilization.
Biomedical and Robotics Applications
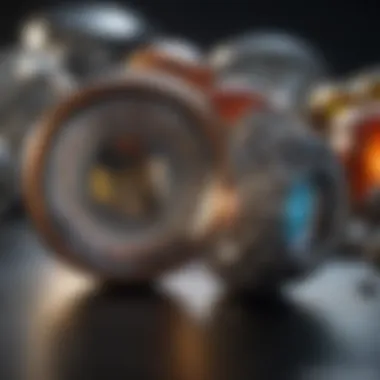
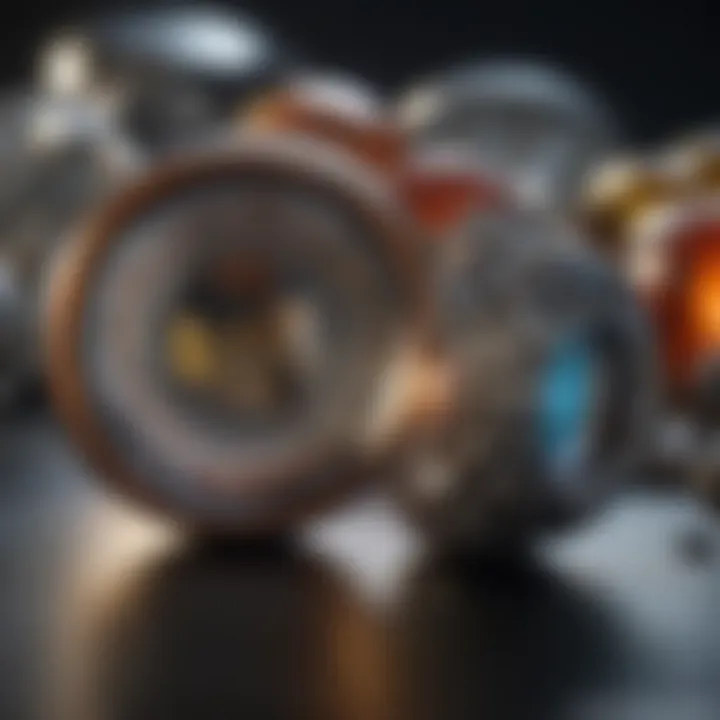
In the realm of biomedical and robotics applications, shape memory alloys showcase their versatility and reliability in intricate mechanisms and surgical instruments. Their key characteristic lies in their biocompatibility and programmable shape memory, enabling innovative solutions in medical devices and robotic systems. This unique feature makes them a favored choice for applications requiring precise motion control and biocompatible materials. Despite their advantages, the specialized training and expertise needed for working with shape memory alloys are essential aspects to navigating their complexities.
Magnetic Alloys
Magnetism and Applications
Magnetic alloys present a captivating fusion of magnetic properties that find versatile applications across electrical machinery and sensors, underscoring their significance in modern technology. The key characteristic of these alloys is their magnetic strength and stability, facilitating efficient energy conversion and sensor functionality. This desirable feature makes magnetic alloys a preferred choice for creating advanced electrical components and sensitive sensors in various industries. However, the susceptibility of magnetic alloys to environmental factors and their magnetic saturation limits require careful calibration in specific applications.
Electrical Machinery and Sensors
Within the domain of electrical machinery and sensors, magnetic alloys demonstrate their prowess in enhancing electronic systems' performance and sensitivity. Their key characteristic lies in their ability to generate magnetic fields with precision and consistency, ensuring optimal functionality in diverse electronic devices. This advantageous feature positions magnetic alloys as a popular choice for manufacturing high-performance electrical components and intricate sensor technologies. Despite their numerous advantages, the susceptibility to demagnetization and magnetic hysteresis should be considered when integrating magnetic alloys into intricate electronic systems.
Industrial Significance
In this article, the section on industrial significance plays a crucial role in highlighting the fundamental importance of metal alloys in various manufacturing processes. Metal alloys are essential components in a wide array of industries, including automotive, aerospace, construction, and electronics. These alloys offer a unique combination of strength, durability, and versatility that make them indispensable in modern manufacturing. By understanding the industrial significance of metal alloys, one can appreciate their role in shaping the technological landscape of today and tomorrow.
Role in Manufacturing
Structural Components
Structural components made from metal alloys are the backbone of many industrial applications. These components provide the necessary strength and stability required for building robust structures, machinery, and equipment. The key characteristic of structural components is their ability to withstand heavy loads and extreme conditions without compromising structural integrity. This makes them a popular choice for industries where safety and reliability are paramount. Despite their strength, structural components can be tailored to be lightweight, which is a significant advantage in industries such as aerospace and automotive where weight reduction is critical for improving performance and fuel efficiency. However, one disadvantage of structural components is the potential for corrosion in certain environments, requiring protective coatings or alloy selection considerations.
Tooling and Machining
Metal alloys are also extensively used in tooling and machining processes due to their exceptional hardness, wear resistance, and thermal conductivity. The key characteristic of tooling and machining alloys is their ability to maintain sharp cutting edges and withstand high temperatures generated during the machining process. This makes them a beneficial choice for precision machining operations where tight tolerances and high surface finish are essential. Additionally, the unique feature of these alloys lies in their machinability, allowing for complex shapes and intricate designs to be efficiently produced. However, one drawback of tooling and machining alloys is their tendency to work-harden during cutting, necessitating appropriate machining strategies to prevent tool wear and ensure dimensional accuracy.
Innovations in Alloy Development
Advancements in Material Science
Advancements in material science have revolutionized the development of metal alloys, leading to the creation of alloys with enhanced properties and performance characteristics. The key characteristic of these advancements is the ability to precisely control alloy compositions at the atomic level, resulting in tailored microstructures that exhibit superior mechanical and chemical properties. This precision engineering has enabled the design of alloys with high strength-to-weight ratios, excellent corrosion resistance, and improved thermal stability, making them a popular choice for demanding applications. One unique feature of advancements in material science is the ability to create custom alloys for specific industrial needs, optimizing performance and efficiency. However, a challenge in alloy development is the need for extensive testing and validation to ensure the desired properties are achieved consistently across production batches.
Tailored Properties for Specific Applications
Tailored properties in metal alloys are designed to meet the exact requirements of specific industrial applications, offering a customized solution for each unique use case. The key characteristic of tailored properties is their ability to fine-tune mechanical, thermal, and chemical properties to suit the intended application, providing optimal performance and longevity. This customizability makes tailored alloys a beneficial choice for industries where standard alloys may not meet the desired specifications. The unique feature of tailored properties lies in their flexibility, allowing manufacturers to optimize alloys for different combinations of strength, ductility, and corrosion resistance as needed. However, one challenge of tailored properties is the complexity of alloy design and the potential trade-offs between different property enhancements, requiring careful consideration to achieve the desired balance of characteristics.