Understanding the Importance of Bench Pins in Jewelry Making
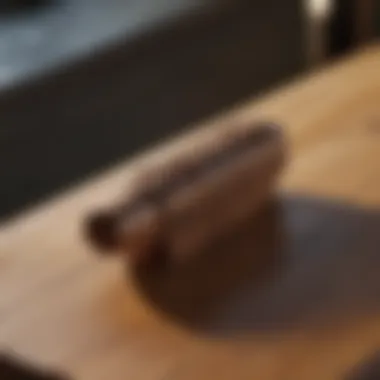
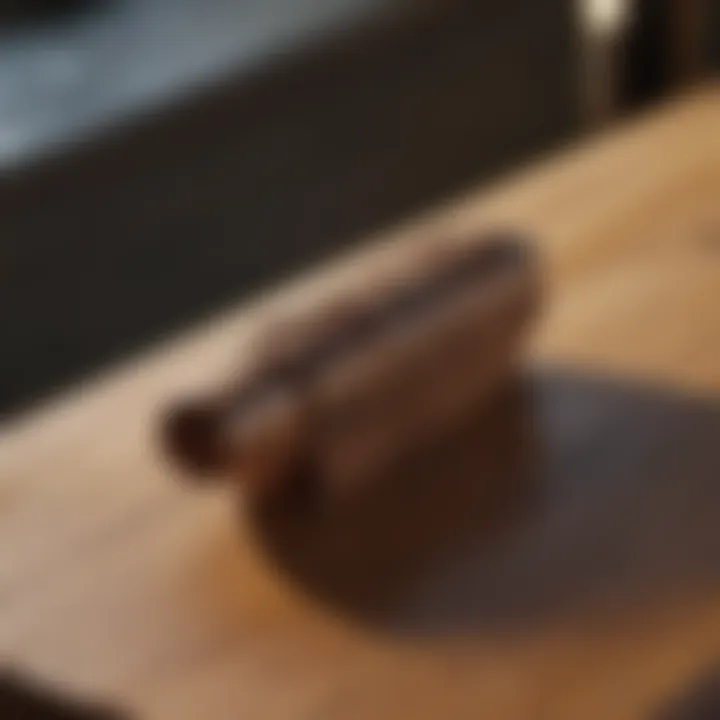
Intro
In the world of jewelry making, every little detail counts. From the sparkling gemstones to the intricate craftsmanship, making a piece of jewelry involves precision and skill. One might easily overlook a small yet pivotal tool in this process: the bench pin. This unassuming accessory is not just an add-on but a crucial element that influences the efficiency and quality of a jeweler's work.
Understanding Bench Pins
Bench pins serve as a sturdy workstation, allowing jewelers to secure their pieces while working. They are designed to accommodate various tasks, such as sawing, filing, and polishing. Different types cater to the specific needs of both professionals and hobbyists, showcasing versatility that is essential for all levels of expertise.
The significance of bench pins transcends mere functionality. An experienced jeweler often builds a relationship with their bench pin, tailoring its setup and position to their crafting style. It’s not just about having a tool; it’s about having the right tool for the task at hand.
The Advantages of Using Bench Pins
Using a bench pin comes with a host of benefits:
- Stability: A well-placed bench pin provides a solid base for intricate work.
- Ease of Use: It simplifies many tasks, making it easier to cut, shape, or solder materials.
- Improved Precision: The stability afforded helps in executing detailed designs without wobbling or errors.
"A jeweler without a bench pin is like a carpenter without a workbench. One cannot craft precision without the right foundation."
Choosing the Right Bench Pin
Selecting the appropriate bench pin is paramount. Here are some considerations:
- Material: Bench pins come in various materials like wood, plastic, or metal. Each offers its unique feel and utility.
- Shape and Size: Depending on the intended use, the shape can affect the ease and comfort of work.
- Adjustability: Some pins allow for adjustments in angle or height, which can be beneficial for certain techniques.
When embarking on your jewelry-making journey, it pays dividends to invest time in finding a bench pin that resonates with your crafting style.
Maintaining Your Bench Pin
As with all tools, maintenance is key to ensuring longevity and functionality. Here’s how you can keep your bench pin in prime condition:
- Regular Cleaning: Remove debris or metal shavings that accumulate from use.
- Check for Wear: Inspect for any damages or wear that might affect performance.
- Support with Padding: If necessary, add padding to enhance comfort when working on harder materials.
Final Thoughts
To summarize, bench pins may seem like an afterthought, but they play a central role in the art of jewelry making. Familiarizing oneself with their uses, types, and maintenance can uplift one’s craft from amateur to expert. As jewelers, embracing these essentials can indeed pave the way for crafting truly remarkable pieces.
Understanding Bench Pins
In the craft of jewelry making, bench pins are often regarded as unsung heroes. These simple yet vital tools hold considerable importance when it comes to achieving precision and efficiency in the creative process. Their very purpose lies in providing a sturdy surface where jewelers can work on various tasks, from shaping and filing metals to setting stones. Understanding bench pins, therefore, means recognizing their role not just as an accessory but as an integral component that enhances the overall quality of jewelry creations.
Definition and Purpose
A bench pin is essentially a flat piece of material, commonly made from wood or metal, that is secured to the workbench. Jewelers use it as a support when performing tasks such as sawing, soldering, and filing. The purpose goes beyond mere convenience; it enables artists to maintain control over their work, ensuring that intricate details are executed with the utmost care. Having a robust and reliable surface can mean the difference between a seamless creation and a frustrating mishmash of pieces.
Consider the process of soldering, for instance. When a jeweler joins two metal pieces together, the bench pin acts as a resting platform that holds the work steady while minimizing movement. This is crucial because even the slightest wiggle can lead to misalignment and ultimately, a less desirable outcome. Therefore, understanding bench pins involves grasping their function in maintaining both stability and precision throughout the crafting journey.
Historical Context
Diving into the history of bench pins reveals their evolution and significance across time. Traditionally, bench pins can be traced back to the early days of jewelry crafting, where artisans fashioned them from whatever materials were readily available. Early bench pins were mostly wooden, often carved from local trees. This simplicity reflected the resourcefulness of tradespeople who relied on natural resources at hand.
Over the course of centuries, as techniques and technologies evolved, so too did the materials and designs of bench pins. Metal alternatives began to emerge along with foldable options, increasing portability and flexibility for jewelers. Each variation tells a story of adaptation, necessity, and innovation—hallmarks of a craft that has withstood the test of time. In understanding bench pins, we appreciate not only their functional aspects but also their rich heritage in the world of jewelry making.
"Jewelry making is not just about the metal; it's about the tools that help bring the vision to life. The bench pin stands at the core of this creative process."
Types of Bench Pins
When it comes to making jewelry, the type of bench pin you use can make a substantial difference in both the quality of your work and your overall experience at the bench. Selecting the right bench pin isn’t just about preference; it’s about function, durability, and adaptability to various tasks you’ll encounter. Each type of bench pin brings its own set of advantages, so understanding these details can elevate your craftsmanship seamlessly.
Traditional Wooden Pins
Traditional wooden bench pins hold a special place in the hearts of many jewelers. Often crafted from hardwoods like maple, these pins are favored for their fine balance of sturdiness and a softer touch on the metal being worked on. In many cases, the natural grain of the wood also provides an aesthetic appeal, giving a quaint charm to the workspace.
Wooden pins typically come in various sizes and shapes, which allows jewelers to choose one that best fits their specific tasks. They are particularly effective when it comes to tasks like cutting, where a little give can prevent breakage of delicate components. Another notable feature is that wooden pins can be easily shaped or modified according to one's personal style, making it a favorite among those who like to customize their tools.
- Pros of Traditional Wooden Pins:
- User-friendly for beginners
- Easily customizable
- Gentler on softer metals
That said, wooden pins do have their drawbacks, such as susceptibility to wear and tear. Regular maintenance is crucial to sustain their performance. A few nicks and dents can cause significant issues in precision work.
Metal Bench Pins
Metal bench pins are gradually gaining traction, particularly among more advanced jewelers who favor durability and sturdiness. Typically made from stainless steel or brass, these pins offer a robust surface that stands up to rigorous wear and tear. They also provide a slick, firm surface which can help with precision work, especially when soldering.
Another advantage is that metal pins are often designed with additional features, such as holes for easy clamping or grooves for better metal support. Jewelers often find that metal bench pins remain true to their shape over time, reducing the need for constant replacement. This makes them an appealing choice for those who view their workbench as an investment rather than just tools.
- Pros of Metal Bench Pins:
- Long-lasting and resilient
- Excellent for precision work
- Less maintenance required
However, the downside is that they can be harsher on softer metals, leading to scratches or damage over time. Jewelers often have to consider their target materials when choosing metal pins.
Foldable and Portable Options
For those who find themselves working in various locations, foldable and portable bench pins provide an ideal alternative. Designed for ease of transport, these pins can be collapsed or easily stored, allowing jewelers to take their craft wherever they go. Whether working at a fair or traveling to a client’s location, these pins make mobility simple.
These typically come in hybrid designs, combining materials like wood and metal to ensure that they maintain a balance of durability with lightweight functionality. Some even feature adjustable heights or angles, which can cater to different working styles and preferences.
- Pros of Foldable and Portable Bench Pins:
- Travel-friendly
- Versatile designs with adjustable options
- Ability to work in various environments
However, it’s crucial to weigh the portability against stability. Often, these pins may not provide the same level of sturdiness as their fixed counterparts. However, for those who deal with moving around, the convenience they offer can far outweigh their limitations.
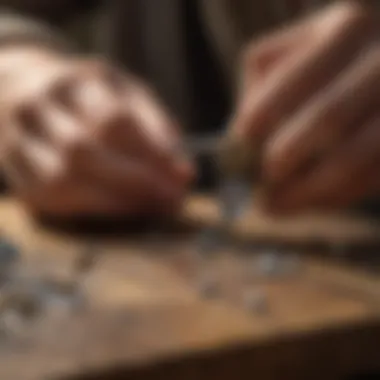
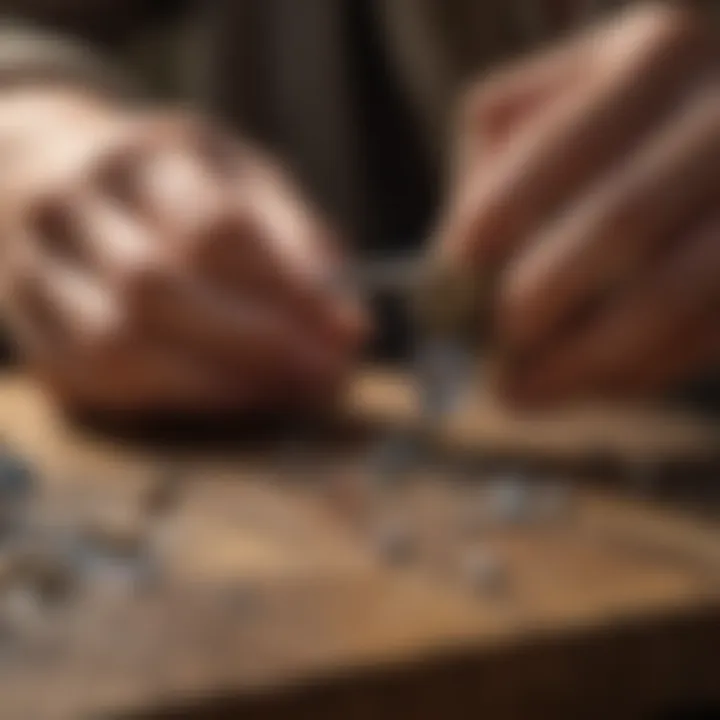
In sum, when choosing a bench pin, it’s vital to consider the advantages each type has to offer in relation to your jewelry-making style and needs. By matching your tool to the job at hand, you not only improve the efficiency of your work but also the pleasure of creating. Remember, the right bench pin is your companion in the journey of crafting beautiful pieces of jewelry.
Materials Used in Bench Pin Construction
The material choice behind bench pins plays a crucial role in their function and longevity. Selecting the right kind of material directly influences the effectiveness and efficiency of the jewelry-making process. Understanding the differences in materials helps jewelers tailor their bench pins to their specific needs, enhancing overall craftsmanship. From wooden pins that trace back to ancient traditions to modern synthetic materials, each option brings unique benefits and considerations.
Wood Varieties
Wood has been a long-standing choice for bench pins primarily because of its availability and workability. Commonly used types include maple, birch, and walnut.
- Maple: Known for its durability and hard surface, maple bench pins resist wear, maintaining their shape over time. This is particularly beneficial for tasks like cutting and filing, where a solid support is essential.
- Birch: Birch is lighter than maple, making it easier to manage. It's also less expensive, which might appeal to beginner jewelers or those on a tight budget.
- Walnut: While on the soft side compared to maple, walnut offers a rich color, adding an aesthetic appeal to workspaces. However, the softer surface might not sustain heavy-duty operations as well as denser woods.
Each wood type comes with its own quirks; for example, some might absorb moisture and expand, influencing precision during intricate tasks. Additionally, jewelers should be aware of the woodworking finishes that can impact the adhesion of materials in soldering tasks.
Metal Alloys
Metal bench pins serve a different purpose and are typically favored for soldering tasks. The sturdy nature of metals provides an unparalleled stability that wood might lack.
- Copper Alloys: Copper pins can withstand extreme heat during soldering while dissipating it at a rapid rate. This reduces the risk of warping or damaging adjacent pieces.
- Steel Pins: Often sourced from high-carbon steel, these pins boast high tensile strength and resistance to bending. They are ideal for hands-on work where durability is needed.
- Brass: While slightly softer, brass pins can help avoid contaminating solder seams due to their lower melting point. They lend a warmth to the workspace aesthetic as well.
Advantages of metal pins include their ability to endure repeated use, but they tend to be heavier than their wooden counterparts, which could be a factor for those looking for lighter tools.
Synthetic Materials
The rise of synthetic bench pins marks an innovative step in the jewelry-making landscape. These materials are engineered to blend performance with versatility.
- Plastic Composites: Lightweight yet durable, plastic composites offer an alternative for jewelers who prioritize ease of use. They're less likely to mar the surface of delicate pieces they hold.
- Polyurethane: Known for their shock absorbance, polyurethane pins cushion impacts, thereby protecting both the bench pin and the workpiece. This is particularly important in high-precision work, as it minimizes vibrations that might affect craftsmanship.
- Silicone-based Materials: These can provide unique levels of grip and flexibility while still being resistant to heat.
Synthetic bench pins are also remarkably easy to clean and maintain, a significant factor for those who frequently work with various materials that might leave residues or tarnish.
Understanding the interplay of these materials helps jewelers not only optimize their tools but also enhance their overall craftsmanship, finding the right match for their unique artistic needs. Each material type—wood, metal, or synthetic—has its own strengths and applications designed to meet the exacting standards of modern jewelry making.
In summary: The material choice for bench pins is not merely a matter of preference but one that profoundly impacts the outcomes in jewelry craftsmanship.
Bench Pin Applications
Bench pins are vital tools that fulfill various specialized functions in the jewelry making process. By creating a stable, secure workspace, bench pins facilitate the intricate tasks that define the craft. Their applications extend across multiple techniques, enabling jewelers to achieve precision and quality in their creations.
Soldering Techniques
Soldering is an essential technique in jewelry making, where metal parts are joined together. The bench pin serves as a solid platform that supports the piece being soldered. The stability provided by the pin allows jewelers to manipulate small pieces easily, ensuring an even flow of solder. When soldering, it's important to place the piece on the pin at an angle that minimizes the risk of accidental movement. This type of careful positioning not only enhances control over the soldering process but also reduces the chances of making costly mistakes. Using a bench pin during soldering leads to cleaner joints and less cleanup work.
"Using a bench pin is like having a reliable partner in the soldering process; it holds everything steady while you do the delicate work."
Cutting and Filing
Cutting and filing are crucial steps in refining the shapes of metal pieces before final assembly. A bench pin accommodates the workpiece efficiently, allowing jewelers to apply their cutting tools with precision. The design of the bench pin often includes a notch, a small cutout that holds the metal securely in place during cutting. This prevents slipping and ensures a straight edge is achieved every time. Additionally, jewelers can work on their pieces at a comfortable height, promoting better ergonomics and reducing fatigue.
This process is critical, as imprecise cutting can throw off the entire design. By utilizing a bench pin, you not only make the cutting more manageable but also improve the overall craftsmanship of your jewelry.
Setting Stones
Setting stones is perhaps one of the most intricate aspects of jewelry making, and having a reliable surface like a bench pin is paramount. When setting a stone, the jeweler needs to manipulate both the metal and the stone carefully. The bench pin acts as a stabilizer, allowing for minor adjustments and precise movements needed for a perfect fitting.
The angle and position at which the jeweler holds the stone can significantly affect the outcome; hence, a bench pin serves to provide leverage and support. The sturdy base aids in minimizing vibrations, a crucial factor when working with delicate gemstones.
Choosing the Right Bench Pin
Selecting the appropriate bench pin is like choosing the right tool for a specific job—it makes all the difference. When faced with an array of options, each tailored for different functions, it becomes crucial to know what factors weigh into making a sound decision. The right bench pin can enhance not just your work efficiency but also the quality of your finished pieces. Hence, taking the time to carefully evaluate your choices can greatly influence your crafting journey.
Factors to Consider
When deciding on a bench pin, several elements should be taken into account. Understanding these factors can help streamline your decision-making process and ensure that you end up with a tool that meets your needs:
- Material: Different materials offer various durability, flexibility, and maintenance needs. For instance, a wooden bench pin might provide warmth and a good grip, while a metal pin could offer longevity and sturdiness.
- Thickness and Size: The size of the pin affects how you can use it—if it's too thick, it might hinder maneuverability; if too thin, it might not hold workpieces properly. Find a balance that suits your working style.
- Shape and Design: Some pins come with unique shapes that cater to specific tasks. Curved or customized shapes might offer better support for certain types of jewelry pieces. A design that fits naturally with your working method can enhance your crafting experience.
- Portability: If you are someone who likes to take their work on the go, consider foldable or lightweight bench pins. They can save space and make it easier to transport your tools.
Evaluating these factors can help you pinpoint which bench pin aligns with your desired functionalities.
Personal Preferences
Even as technical specifications and practicalities play an immense role, personal preferences cannot be overlooked. Your own crafting style, comfort, and working environment should guide your choice:
- Comfort Level: Think about how each pin feels in your hand while working. A pins that causes strain can detract from your concentration.
- Aesthetic Appeal: Some jewelers are inspired by the beauty of the tools they use. The design and finish of a bench pin can enhance the overall experience of making jewelry.
- Previous Experiences: Reflect on your past usage of different types of pins. If a certain style or material has worked better for you previously, it might be worth sticking with that.
- Intended Projects: What kind of jewelry are you planning to make? The complexity of your projects can dictate your needs. If you’re working with intricate designs, a more specialized pin may suit those demands better.
"Choosing the right bench pin not only improves efficiency but can also deepen your enjoyment and satisfaction in the making of jewelry."
Making the right choice for a bench pin is not just about functionality; it’s about creating a workspace where your creativity can flourish, leading you toward masterpieces you can be proud of.
Bench Pin Maintenance
Maintaining your bench pin is crucial in jewelry making. A well-cared-for bench pin enhances the lifespan of your tools and improves the quality of your craftsmanship. Dull or dirty bench pins can hinder precision and may lead to mistakes in your work. Knowing how to keep your bench pin in good shape can save you both time and frustration when creating jewelry pieces that require the utmost attention to detail.
Cleaning Techniques
Regular cleaning of your bench pin keeps it free from debris and residues from the materials you work with. Here are essential cleaning techniques to adopt:
- Use a Soft Brush: A fine brush can gently sweep away dust and shavings. This is especially important if you’re using materials like wood, where tiny particles can create a rough surface on your pin.
- Apply Soapy Water: Occasionally, it’s useful to dip a soft cloth into soapy water and wipe down the surface of your bench pin. This helps in removing stubborn dirt or oxidation, particularly on metal pins. Remember not to soak your bench pin; just dampen the cloth enough for a thorough wipe.
- Dry Thoroughly: After cleaning, it’s crucial to dry the bench pin completely. Leaving moisture can cause wood to swell or metal to rust. A soft, lint-free towel can do the trick here.
- Protect with Oil: For wooden pins, using a light mineral oil after cleaning will help in maintaining their condition. It nourishes the wood, making it less prone to cracking or splintering.
By including these cleaning habits into your routine, you're ensuring that your bench pin continues to perform at top-notch levels.
Storage Solutions
Proper storage of your bench pin not only protects it from damage but also helps maintain an organized workspace. Here are some effective storage solutions to consider:
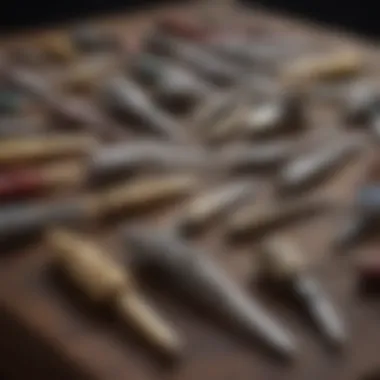
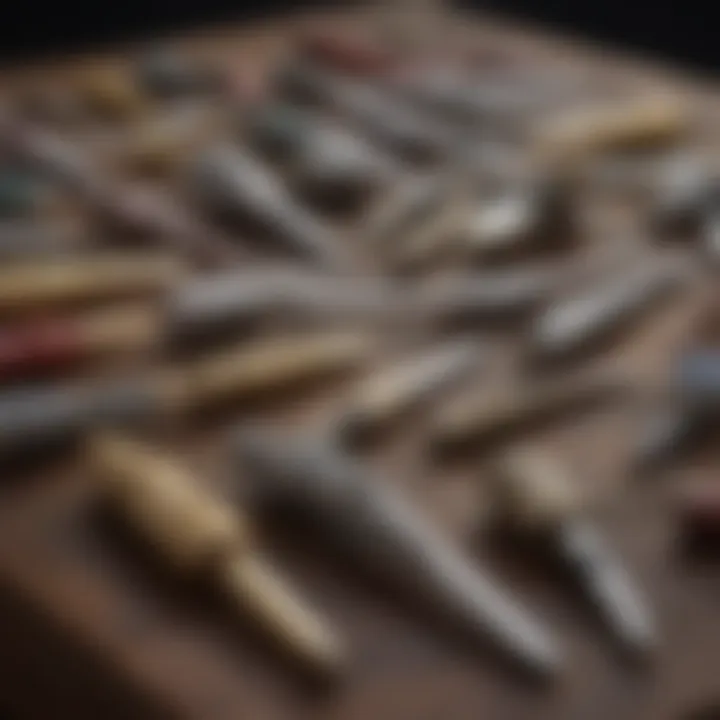
- Dedicated Workspace: Always have a designated area where your bench pin resides. This minimizes the chance of it getting knocked over or damaged during your jewelry-making process.
- Use a Tool Holder: Consider placing your pin in a wall-mounted tool holder. This keeps it off the surfaces while making it easily accessible when you need it.
- Wrap It Up: If you have a foldable or portable bench pin, storing it in a padded pouch or case prevents scratches and damages during transport.
- Maintain Environment: Keep the area where your bench pin is stored at a controlled temperature and humidity. Abrupt changes in environment can warp or damage the material.
Overall, taking the time to clean and store your bench pin properly pays off in the long run. This ensures optimal performance and prolongs the life of this essential tool in your jewelry-making toolkit.
Maintaining your bench pin is as important as the craft itself. A well-kept pin can mean the difference between a masterpiece and a mishap.
Innovations in Bench Pin Design
Innovations in bench pin design are transforming the landscape of jewelry making. These advancements play a pivotal role in enhancing the efficiency, comfort, and versatility of jewelers’ workstations. As the industry evolves, so do the tools and equipment that aid artisans in creating intricate pieces. When discussing bench pins, it's essential to focus on specific elements that signify progress and offer genuine benefits to those in the trade.
Modern Features
With technology advancing at breakneck speed, one can find bench pins equipped with numerous modern features. For instance, some of the latest bench pins come with integrated jaws or clamps. These allow jewelers to hold their work securely without needing additional tools. Among the noteworthy features:
- Adjustable Heights: Customizable height settings help jewelers work at their preferred level, reducing strain on the back and neck.
- Built-in Measurement Guides: Markings for quick measurements are often included, allowing artisans to make precise adjustments as they work.
- Magnetic Surfaces: Some modern bench pins have magnetic strips that hold small metal pieces, minimizing the risk of losing essential components. These innovations contribute significantly to achieving that much-needed precision in craftsmanship.
Moreover, the rise of smart bench pins is notable. These advanced systems may have Bluetooth connectivity, enabling users to access tutorials or guides directly. This incorporation of technology could help beginners and seasoned jewelers alike enhance their skills while working more efficiently.
Ergonomic Improvements
The ergonomics of bench pins cannot be underestimated. In the quest for well-crafted jewelry, the comfort of the jeweler is of utmost importance. Several ergonomic improvements have been integrated into contemporary designs that support the user's posture and reduce fatigue.
An example worth mentioning includes bench pins molded to fit the natural curve of the hand. This contributes to less strain when filing or soldering, which can be intensive tasks. Additionally:
- Soft-Grip Materials: Many bench pins now feature soft-grip surfaces that ensure the user has a firm handle, preventing slips that could lead to accidents.
- Rotatable Bases: Some bench pins can be rotated, allowing users to access different angles without shifting their bodies or their workpieces.
- Padding and Cushions: Certain designs incorporate padding that helps in reducing pressure on the wrist and forearm, making long working hours much more bearable.
An ergonomic bench pin can mean the difference between a few hours of creative bliss and unbearable stiffness that lasts for days.
In summary, innovations in bench pin design encompass not just technological features but also essential ergonomic advancements that cater to a jeweler's comfort. These enhancements notably impact craftsmanship quality and the jeweler's overall experience, ultimately leading to higher satisfaction and better productivity.
The Impact of Bench Pins on Jewelry Quality
Bench pins play a pivotal role in determining the quality of crafted jewelry. They provide jewelers with a stable work surface, allowing for precision and control during various stages of the jewelry-making process. Having a reliable bench pin can mean the difference between a well-made piece and one that appears sloppy or unrefined.
Precision in Craftsmanship
Crafting jewelry requires a keen eye and steady hands, but this is where the bench pin comes into play. By supporting the workpiece, bench pins allow jewelers to position their materials firmly. This stability is essential especially during cutting, filing, and soldering. When a jeweler's work surface is stable, it leads to improved accuracy in measurements and placements.
For instance, when setting a stone, the jeweler must make precise cuts and adjustments. If the piece is wobbling or moving unexpectedly because of an unstable surface, this precision is jeopardized. A good bench pin enables fine detail work, enhancing the overall look and integrity of the finished product. If a piece is crafted with care and precision, it reflects the skill and dedication of the jeweler, elevating the quality of the work significantly.
There are several techniques jewelers can adopt to improve their skills while using bench pins:
- Consistency in Pressure: When using tools like a saw or file, the amount of pressure should remain consistent to ensure smooth finishes.
- Correct Angle Positioning: Frequently adjusting the position of the piece in relation to the bench pin enhances the jeweler's ability to achieve accurate cuts and settings.
- Use of Additional Aids: Employing clamps can increase control over materials, further adding to the precision of the task.
Effects on Finished Products
The effects of using bench pins extend beyond just the act of crafting. When quality craftsmanship meets appropriate bench tools, the outcome is a polished piece of jewelry that can stand the test of time. A well-crafted product not only appeals to the buyer’s aesthetic sense but also often holds greater value — both sentimental and monetary.
The aspects that contribute to this high quality include:
- Structural Integrity: Jewelry that has been properly soldered and assembled on a stable work surface exhibits fewer weaknesses. This longevity is appreciated by both makers and wearers alike.
- Finish Quality: A well-finished product will show fewer signs of rough edges or misalignments, creating a more professional appearance. This is crucial, especially in pieces meant for special occasions, like rings for engagements or weddings.
- Market Competitiveness: Jewelers who produce high-quality items using reliable tools can gain an edge over competitors. Consumers are often willing to pay a premium for pieces that demonstrate superior craftsmanship and durability.
A reliable bench pin is not just a tool in the jewelry-making arsenal; it is a vital component that enhances the overall quality of the work produced.
In summary, the impact of bench pins on the quality of jewelry can be observed in both the craftsmanship process and the final products. Their importance can't be overstated, and understanding their role can help jewelers elevate their craft, ultimately leading to greater customer satisfaction and success in the jewelry market.
Bench Pin Accessories and Tools
Bench pins do not always stand alone; they thrive on accessories and tools that enhance their functionality and versatility in the jewelry-making process. When you consider the many intricacies of creating jewelry, you begin to realize just how crucial these additional elements become. Without the right accessories, using a bench pin can limit your efficiency and the quality of your work.
Clamps and Holders
Utilizing clamps and holders is crucial for achieving precision in jewelry making. These tools serve to secure your workpieces firmly in place on the bench pin, preventing unwanted movement or slipping. There are various types of clamps available – some resemble a more traditional C-clamp, while others are designed specifically to affix directly onto the bench pin itself. Each type has its own advantages, and choosing the right one can make a significant difference.
- Versatility: Some clamps allow you to work on intricate designs by keeping multiple pieces secured together.
- Safety: With a firm grip on your materials, you can avoid mishaps such as accidental slips that may harm your fingers or damage materials.
- Improved Efficiency: Instead of constantly adjusting your materials, a good clamp helps you focus on the craft at hand once it's secured.
Holders, on the other hand, are designed to accommodate specific shapes or sizes of gemstones or metal sheets. These can make dull tasks like setting stones easier, providing a stable foundation for careful work.
Cutting and Finishing Tools
The right cutting and finishing tools are indispensable when dealing with bench pins in jewelry making. These tools help transform raw materials into finished, sought-after products.
- Cutting Tools: For those requiring precise cuts, a jeweler’s saw is one of the most favored options. It allows for intricate designs, easily cutting through metal or other materials while ensuring clean edges.
- Finishing Tools: After cutting, the finishing process is where the magic happens. Tools such as files, sanders, and polishing machines will refine the surface and eliminate rough edges, creating a smooth finish that enhances the piece's overall aesthetic appeal.
"The right tools not only increase efficiency but also amplify the joy in creating jewelry. A well-finished piece sings with quality and artistry, engaging both the maker and the wearer."
Bench Pins in Contemporary Jewelry Design
In the rapidly evolving realm of jewelry making, bench pins have cemented their status as indispensable tools for contemporary designers. As jewelers continue to push the envelope of creativity, these pins serve not just as work surfaces but also as platforms for innovation. Let’s explore how modern jeweler’s adapt these bench pins, the significance they carry, and some illuminating case studies that highlight their relevance.
Adaptation by Modern Jewelers
Modern jewelers have embraced bench pins with a unique twist. Whereas traditional designs focused primarily on functionality, today's designs reflect an integration of ergonomics and aesthetics.
- Ergonomic Adjustments: Many jewelers are now opting for adjustable bench pins that promote better posture, helping prevent strain during long hours of work. An excellent example is the Benchtop Workbench with Adjustable Bench Pin made by Grobet USA. It allows for a customizable setup tailored to individual needs.
- Innovative Materials: Metal alloys and high-density plastics are increasingly being utilized in bench pin construction. This shift not only enhances durability but also contributes to a cleaner work surface. These materials provide a stark contrast to the traditional wooden options, often making them more suitable for modern soldering techniques.
- Integration of Technology: Some contemporary designs even incorporate technology such as built-in LED lights or magnetized surfaces for holding tools securely. This fusion of form and function reflects the demands of today’s jewelers who require speed and precision.
The clever combination of these features is what makes bench pins stand out in today’s jewelry design.
Case Studies
To provide a clearer picture, let's look at a few specific instances where bench pins have played a pivotal role in modern jewelry making, showcasing their versatility and impact.
- Sophie Wong’s Studio: Sophie Wong, an up-and-coming designer, utilizes a crafted metal bench pin to seamlessly integrate her intricate designs into her workflow. The adjusted height and angle allow her to work comfortably for extended periods without compromising on creativity.
- Katherine Dwyer Jewelry: This brand is known for producing unique gemstone rings using a foldable bench pin. The ease of portability allows Katherine to conduct workshops, sharing her craft with aspiring jewelers while demonstrating the flexibility and utility of her equipment.
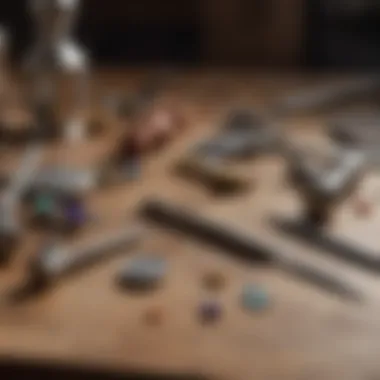
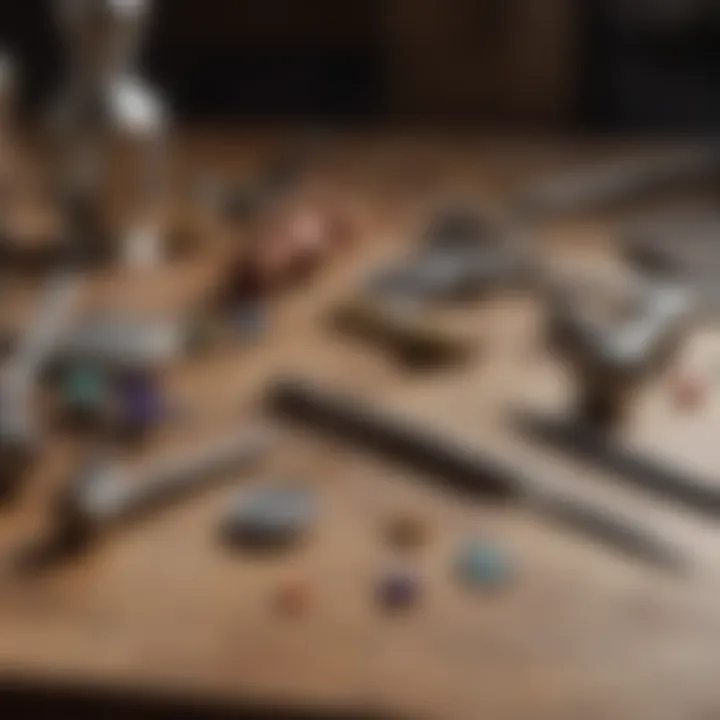
"Bench pins are not just tools. They are the silent partners in the process of creation, allowing ideas to take shape in the physical realm."
- Global Jewels Collective: An organization of various artistic jewelers has started employing acrylic bench pins, providing a non-stick surface for soldering intricate pieces. This has markedly improved the final product quality, as the reduced oxidation and ease of cleaning increase the longevity and finish of the jewelry.
These examples illustrate not only the adaptation of bench pins but also how they enhance the artistry and functionality within this creative sphere. As we peel back the layers of contemporary design, it is clear that bench pins are evolving alongside the jewelers who wield them, ensuring that they remain relevant and indispensable.
Learning from Experienced Jewelers
Learning from seasoned jewelers offers immense value in mastering the art of jewelry making. As every art form evolves, so too does the methodology behind it. Experienced jewelers have likely navigated numerous challenges and cultivated a wealth of techniques that can significantly improve one’s craft. Gathering knowledge from these artisans not only accelerates one's learning curve but also provides insights into overcoming obstacles faced during the jewelry creation process.
Engaging with skilled jewelry makers allows enthusiasts to grasp the nuanced art of using bench pins effectively. These interactions can happen through workshops, seminars, or even informal discussions at local gemstone or jewelry clubs. The specific techniques shared by these experts often encompass techniques developed over years of experimentation and innovation. They offer real-world applications that might not simpley surface in textbooks.
Techniques and Tips
- Take Advantage of Visual Learning
A great tip provided by jewelry veterans is to watch them as they work. Observing their hand movements, the precision of their cuts, and the angles they achieve can be enlightening. Some jewelers might employ unusual twists or grips of their tools that can aid in stabilizing pieces during soldering or setting. - Practice Patience
It's easy to become caught up in the excitement of creating jewelry but remember, jewelry making is akin to a fine wine; it benefits from patience. Seasoned jewelers often emphasize the importance of taking one’s time with each step, especially when using tools like bench pins. Rushing often leads to mistakes. - Experiment with Different Bench Pins
Different projects might require various bench pin styles. Ask experienced jewelers about their preferred choices and why they opt for them in particular scenarios. This is where personal preferences come into play, and you can gather useful insights on testing and trying out new products.
Common Challenges
Even the most skilled jewelers encounter hurdles; it’s part of the journey. Understanding these common challenges allows new crafters to sidestep potential pitfalls. Here are some frequent struggles experienced jewelers often face:
- Precision Alignment
Achieving accurate alignment while using a bench pin can be tricky. Beginners might inadvertently angle a piece improperly, affecting the overall design. Seasoned jewelers suggest marking the bench pin with guidelines to serve as a visual aid during cutting or filing, ensuring a cleaner finish. - Tool Maintenance
Bench pins become experienced tools themselves, each gathering nicks and wear over time. Veteran jewelers recognize that maintaining these pins' condition is crucial for quality work. Repair or replacement is often necessary, and understanding when to take that step can be quite a learning curve for newcomers. - Managing Material Behaviors
Each type of material behaves differently. Understanding how metals will react based on thickness, type, or even atmospheric conditions often takes experience. Some materials may expand when heat is applied, leading to unexpected issues in soldering. Jewelers can share anecdotes of projects gone awry because of misjudged material properties. Learning these behaviors through their stories enhances your own practice.
“There’s no substitute for the hands-on knowledge you gain from those who've been in the trenches. Every struggle they recount is a lesson for you.”
In summary, the journey of a jeweler is paved with learning, sharing experiences, and overcoming common obstacles. By listening and engaging with experienced artisans, newer jewelers can enrich their understanding, refine their skills, and ultimately create exquisite jewelry with confidence.
Bench Pins Across Cultures
The significance of bench pins stretches far beyond their basic function in jewelry making; its cultural reflections and variations illustrate the adaptability and creativity inherent in artisan practices worldwide. In different corners of the globe, jewelers have tailored their bench pin designs and usages to unique cultural contexts, molding the tools of their trade into symbols of local craftsmanship and innovation.
Global Variations
Across various cultures, the construction and design of bench pins often reflect local customs, available materials, and specific artistic traditions. For instance, in Japan, bench pins might be crafted from local cedar wood, renowned for its durability and aroma, blending functionality with a deep appreciation of nature. Jewelers in Italy, on the other hand, might prefer more ornate metal designs, perhaps employing brass or bronze, which not only serve a purpose but also pay homage to the rich history of Italian metalwork.
These variations contribute to a diverse array of techniques and practices. For jewelry makers in India, a heavy, sturdy bench pin aids in the intricate hand-engraving techniques characteristic of traditional Indian jewelry. Meanwhile, bench pins in regions like the Middle East may include intricate carvings that narrate local folklore or religious stories, further enriching the creative expression involved in jewelry making.
- Materials Used:
- Design Appropriateness:
- Local wood types
- Metals like brass, bronze, silver
- Synthetic materials that reflect modern practices
- Simplicity vs. ornamentation
- Adaptation for specific techniques
Cultural Significance
The cultural significance of bench pins transcends mere utility. In many traditions, the tools used for crafting jewelry are seen as extensions of the artisan's identity. In various cultures, the process of jewelry making often involves rituals, and the bench pin becomes a central participant in those practices.
In indigenous cultures, for instance, a bench pin can symbolize connection to ancestry. Jewelers may view their tools as sacred, carrying stories that link back generations. This deep-rooted meaning is often reflected in how the tools are cared for, maintained, and even displayed.
Moreover, the way bench pins are utilized can mirror the values and societal roles of artisans. For example, in societies where jewelry is intricately tied to community status or cultural heritage, the craftsmanship, facilitated by a well-chosen bench pin, becomes a statement of identity.
"The process of creation is often as significant as the finished piece; the tools we use tell as much about us as the jewelry we make.”
As bench pins evolve with modern techniques, understanding their cultural dimensions enriches our appreciation of the craft. Jewelers are not just makers; they are storytellers, weaving cultural narratives and personal journeys into every piece they create.
Future Trends in Bench Pin Usage
In the evolving world of jewelry making, bench pins are more than a mere accessory; they are integral to the crafting process. Understanding the future trends regarding their usage can provide insights and advantages for both budding and seasoned jewelers. As the demand for unique and intricate designs increases, so does the need to adapt the tools we use.
Emerging Technologies
The intersection of jewelry making and technology has birthed some fascinating innovations. One area ripe for progress is the incorporation of smart materials into bench pins. Materials that respond to heat or touch could help jewelers in various ways, such as by indicating an optimal soldering temperature or suggesting the best angle for filing. Imagine a bench pin that alerts you with a subtle vibration when you're about to make a mistake! This could vastly reduce errors, making the crafting process not just easier but also smarter.
Additionally, 3D printing technology is stirring the pot on bench pin designs. Jewelers can create highly customized bench pins tailored to their specific needs with ease. For instance, a jeweler specializing in intricate metalwork might prefer a bench pin with unique grooves or supports designed for their specific projects. The ability to prototype and refine bench pins in digital spaces allows for a deeper creativity that could lead to unprecedented designs and techniques.
Moreover, some companies are experimenting with adding integrated lighting to bench pins. Enhanced visibility can create a more precise work environment. Modern artisans may find that even the slightest adjustment in lighting can influence their detailed work significantly. Utilizing LED technology can illuminate critical areas and prevent shadows that can obscure detail.
Anticipated Changes in Design
As craftsmanship continues to progress, so will the design of bench pins. Traditionally, these tools have been simple slabs of wood or metal but expect to see more ergonomic variations in the near future. With a better understanding of ergonomics, future designs may include adjustable heights or angles to promote better posture. Jewelers spending long hours at the bench often strain their backs and wrists, and adjustable designs could alleviate some of these concerns and promote healthier work habits.
Additionally, materials used in bench pins might transition towards more sustainable options. Environmentally conscious practices in jewelry making are becoming increasingly significant. Jewelers may prefer bench pins made from recycled materials or sustainably sourced woods. This not only aligns with eco-conscious values but may also appeal to customers who are looking for ethically crafted jewelry.
Aesthetic considerations will also emerge. A trend towards minimalism in design could influence bench pins to be sleeker and visually pleasing without sacrificing functionality. Bench pins that seamlessly integrate into a workspace might become the norm, harmonizing with overall design themes in home-based studios or commercial environments.
"As technology strides forward, even the simplest tools like the bench pin can evolve, challenging jewelers to rethink how they craft and create. The future is in adapting to these advancements while honoring the traditions that shaped the craft."
Just as jewelry itself continues to innovate—from artistry to function—so will the bench pin evolve into a pivotal aspect of those transformations.
Culmination
- Versatility: Bench pins adapt to numerous jewelry-making processes, from cutting to setting stones, making them essential for any jeweler’s toolkit.
- Enhanced Craftsmanship: With a stable foundation, jewelers can execute detailed work with greater accuracy, improving overall product quality. This leads to the production of pieces that are not just beautiful but structurally sound.
- User-Centric Design: Innovations such as ergonomic improvements and adaptable designs point to the evolving nature of bench pins, catering to the different needs of jewelers—whether they are hobbyists or seasoned professionals.
"A good bench pin is a jeweler's best companion, offering support and stability when it counts the most."
By recognizing how integral bench pins are to both the craftsmanship and overall quality of the finished pieces, it becomes evident that they hold a vital position in the jewelry-making process. The right selection and maintenance of a bench pin are not mere suggestions, but rather essential practices for enhancing the jewelry-making experience.
Recap of Key Points
To reiterate the main takeaways from the exploration of bench pins:
- Definition and Purpose: Understanding the basic framework and significance of a bench pin in various jewelry-making tasks.
- Types of Bench Pins: Recognizing the different kinds, including wooden, metal, and portable options, offering versatility for multiple applications.
- Materials Used: Each type's construction material influences durability and functionality.
- Applications: Bench pins are crucial in soldering, cutting, and stone-setting enhancing precision in all these processes.
- Selection and Maintenance: Key factors influencing choice, along with crucial maintenance tips to sustain their effectiveness.
- Innovations and Trends: Keeping abreast with modern enhancements can open doors for new techniques and streamlined workflows.
The Continuing Importance of Bench Pins
Even as jewelry-making technology evolves, the essentials like bench pins remain relevant. They are a mainstay that helps to maintain a connection to traditional craftsmanship while still aligning with contemporary practices. Bench pins aren't an optional extra; they are foundational to quality work.
As new tools emerge, the good ol' bench pin adapts and persists, forming the backbone of effective jewelry creation. From classroom training for aspiring jewelers to workshops for experienced artisans, bench pins are likely to keep shining brightly in the jewelers' toolkit for years to come. They remind us that even in the face of change, some tools remain indispensable.
In light of the above, every craftsperson should recognize the worth of investing not only in a good bench pin but also in the knowledge surrounding its optimal use and maintenance. After all, a jeweler with a solid understanding of their tools—especially one as crucial as the bench pin—can transform raw materials into wonderful creations.