Unleashing the Power of Burnout Ovens in Jewelry Making: A Comprehensive Guide
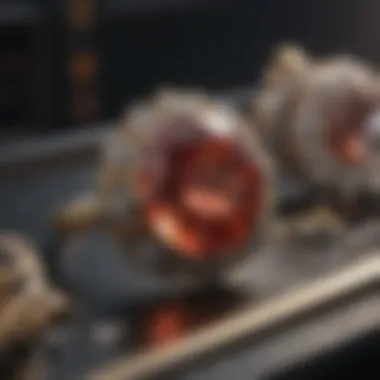
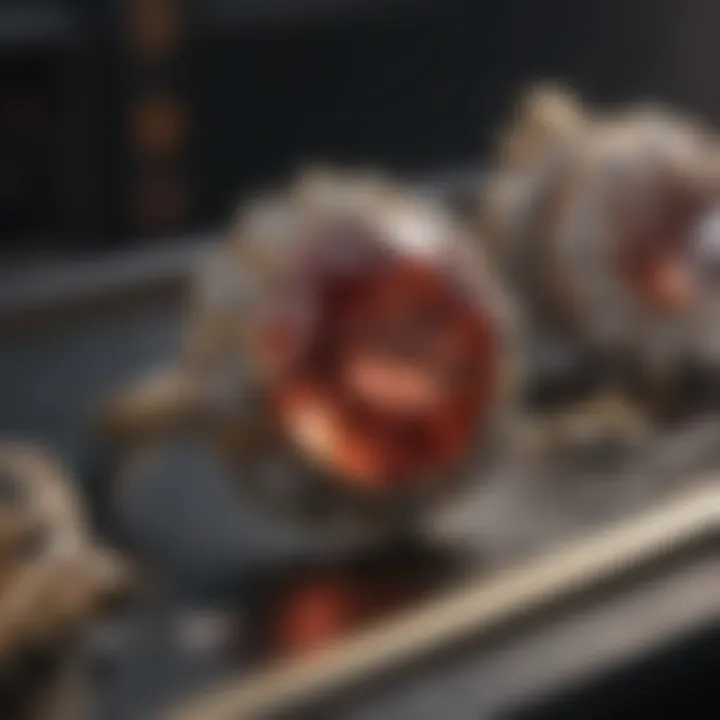
Overview of Gemstones and Minerals
Gemstones and minerals hold a crucial role in the world of jewelry making, serving not only as adornments but also as symbols of status and personality. The history of gemstones and minerals dates back centuries, intertwining with various cultures and societies across the globe. These precious stones have been cherished for their beauty and rarity, making them highly sought after by gemstone enthusiasts, collectors, and jewelry designers alike.
Gemstone Formation and Properties
The process of gemstone formation is a marvel of nature, involving intricate geological forces that transform raw materials into stunning gems. Gemstones are defined by a myriad of properties, including color, hardness, and luster, which determine their value and appeal. These properties play a significant role in classifying gemstones and differentiating them from one another based on their unique characteristics.
Types of Gemstones
Within the realm of gemstones, there exists a distinction between precious and semi-precious varieties, each possessing its own allure and rarity. Common gemstone varieties like rubies, emeralds, and sapphires captivate with their vibrant colors and historical significance. In contrast, exotic and rare gemstones stand out for their scarcity and distinct features, attracting the attention of collectors and connoisseurs in the world of jewelry.
Identifying and Evaluating Gemstones
The value of a gemstone is influenced by various factors, including clarity, cut, and carat weight, which are assessed through specialized techniques for gemstone identification. Gemstone quality is determined by the presence of flaws, color consistency, and overall aesthetic appeal, shaping its desirability in the market. For enthusiasts and professionals, understanding how to evaluate gemstones accurately is essential for making informed decisions and investments.
Caring for Gemstones
Proper care and maintenance are essential for preserving the beauty and longevity of gemstones. Cleaning gemstones regularly and storing them in appropriate conditions help prevent damage and deterioration over time. Additionally, avoiding common mistakes in gemstone care, such as exposure to harsh chemicals or sudden temperature changes, can ensure the durability of these precious stones. By following preservation tips tailored to specific gem types, individuals can protect their gemstone collections and retain their value for generations to come.
Introduction to Burnout Ovens in Jewelry Making
In the realm of jewelry making, burnout ovens stand as indispensable tools, revolutionizing the process of creating exquisite pieces of art. These ovens serve a critical role in the meticulous craftsmanship required for transforming raw materials into stunning jewelry pieces that captivate the beholder's gaze. Understanding the nuances of burnout ovens is key to mastering the art of jewelry fabrication. This section delves deep into the intricacies of burnout ovens, shedding light on their importance in ensuring precision, quality, and efficiency in the jewelry-making process.
Understanding the Role of Burnout Ovens
Principles of Burnout Process
The principles underpinning the burnout process are foundational to achieving desired results in jewelry casting. With precise control over temperature and atmospheric conditions, the burnout process ensures the effective removal of wax or other materials, leaving behind a flawless cavity destined for the molten metal. This meticulous procedure is essential for guaranteeing clean, void-free castings and is a hallmark of professional jewelry making. The unique characteristic of this process lies in its ability to eliminate any residue thoroughly, creating a pristine mold ready for casting.
Imprtance of Proper Temperature Control
The significance of maintaining accurate temperature control cannot be overstated in the realm of jewelry making with burnout ovens. Precise temperature regulation is essential for achieving consistent results during the burnout process, preventing defects and ensuring the successful casting of intricate designs. A key feature of proper temperature control is its ability to enhance the overall quality and longevity of jewelry pieces. The unique advantage it offers lies in its capacity to yield flawless castings, free from imperfections that might arise due to temperature fluctuations.
Materials Suitable for Burnout Process
Selecting suitable materials for the burnout process is crucial for optimizing jewelry fabrication outcomes. Certain materials are tailor-made for the burnout process, ensuring that they can withstand the rigors of high temperatures and transformation into metallic forms. The chosen materials must exhibit burnout characteristics that complement the overall casting procedure, enabling the creation of intricate designs with impeccable detail. This section explores the advantages and disadvantages of various materials commonly employed in the burnout process, shedding light on their optimal applications for jewelry making.
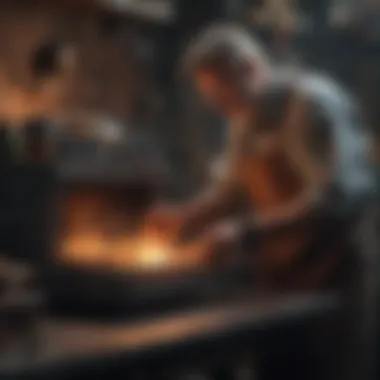
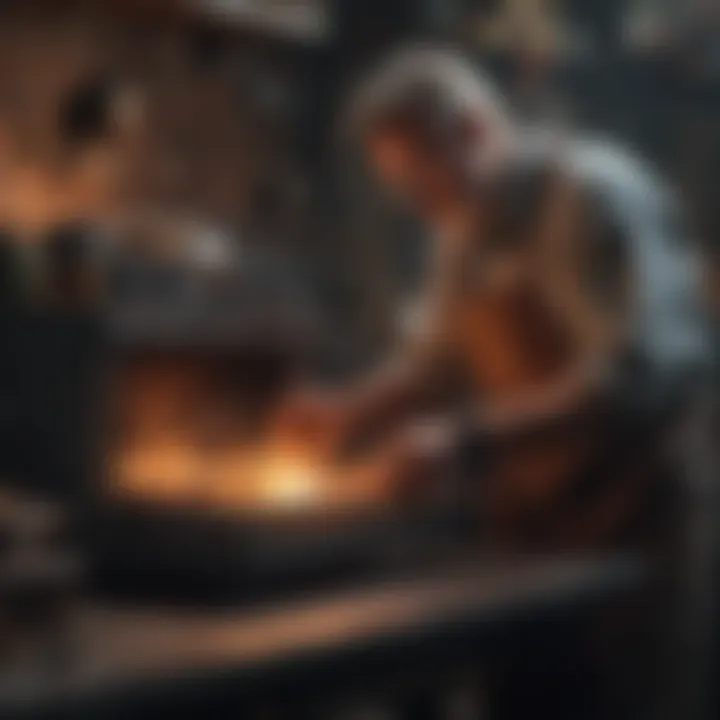
History and Evolution of Burnout Ovens
Traditional Methods vs. Modern Techniques
The evolution of burnout ovens from traditional methods to modern techniques represents a significant leap in the jewelry-making industry. Traditionally, artisans relied on rudimentary ovens with limited capabilities, leading to inconsistencies in casting quality. In contrast, modern techniques leverage advanced technology and innovative designs to achieve unparalleled precision and efficiency in the burnout process. The transition from traditional methods to modern techniques has revolutionized jewelry making, empowering artisans to push the boundaries of creativity and craftsmanship in ways previously unimaginable.
Technological Advancements in Burnout Ovens
Technological advancements have revolutionized the functionality and performance of burnout ovens, elevating them to new heights of efficiency and accuracy. State-of-the-art features such as programmable controls, precise temperature regulation, and enhanced safety mechanisms have transformed burnout ovens into indispensable assets for jewelry designers. The incorporation of advanced technologies has not only streamlined the burnout process but also expanded the creative possibilities available to artisans, setting new standards for excellence in jewelry fabrication.
Benefits of Using Burnout Ovens
Efficiency in Casting Process
The efficiency unlocked by burnout ovens in the casting process is unmatched in the realm of jewelry making. By optimizing the burnout process, artisans can achieve higher productivity levels, minimize material wastage, and expedite the production of jewelry pieces without compromising quality. This enhanced efficiency translates to cost savings and faster turnaround times, providing artisans with a competitive edge in a dynamic market landscape.
Enhanced Precision and Detailing
The nuanced precision and detailing made possible by burnout ovens redefine the standards of craftsmanship in jewelry fabrication. These ovens empower artisans to create intricately designed pieces with microscopic detail, bringing their artistic vision to life with unparalleled clarity. The capacity for precision afforded by burnout ovens opens up a world of creative possibilities, enabling artisans to explore complex designs and techniques that were previously unattainable.
Reduced Risk of Defects
One of the most significant advantages of using burnout ovens is the substantially reduced risk of defects in the casting process. By ensuring optimal burnout conditions and precise temperature control, artisans can mitigate common casting flaws such as porosity, shrinkage, and distortion. This results in a higher success rate for producing flawless jewelry pieces, elevating the overall quality and market appeal of the final products.
Types of Burnout Ovens for Jewelry Making
When delving into the realm of jewelry making, understanding the diverse types of burnout ovens plays a crucial role in ensuring impeccable craftsmanship and precision. Each type of burnout oven - electric, gas, and vacuum - brings its unique set of advantages and considerations to the jewelry fabrication process. These ovens serve as essential tools for jewelry designers and artisans, enabling them to achieve intricate detailing and superior quality in their creations.
Electric Burnout Ovens
Electric burnout ovens stand out for their precise control over temperature and dependable performance, making them a popular choice among jewelry makers. The key feature of electric burnout ovens lies in their digital programmability, allowing users to set and maintain specific temperatures accurately throughout the burnout process. This level of control ensures consistent results and minimizes the risk of defects in casted jewelry pieces. Despite their efficiency, electric burnout ovens may have limitations in handling larger production volumes due to their size and capacity restrictions.
Gas Burnout Ovens
Gas burnout ovens are prized for their robust operating mechanisms and versatility in jewelry production. The main characteristic of gas ovens is their rapid heating capabilities, which accelerate the burnout process for increased efficiency. Jewelry designers often opt for gas burnout ovens for their ability to reach high temperatures quickly, expediting the casting cycle. However, considerations for safety and performance are paramount when using gas ovens due to the combustible nature of the fuel source. Proper ventilation and adherence to safety protocols are essential to mitigate potential risks during operation.
Vacuum Burnout Ovens
Vacuum burnout ovens offer distinct advantages when working with delicate materials and require precise control over the casting process. The standout feature of vacuum ovens is their ability to create a controlled atmosphere, ideal for preventing contamination and achieving flawless casting results. Jewelry makers benefit from the enhanced precision in casting intricate designs and intricate pieces. While vacuum ovens excel in handling fragile materials with care, they may pose challenges in terms of maintenance and operation intricacies.
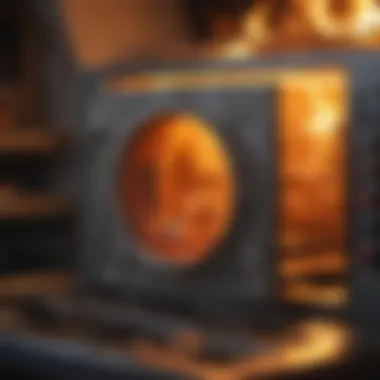
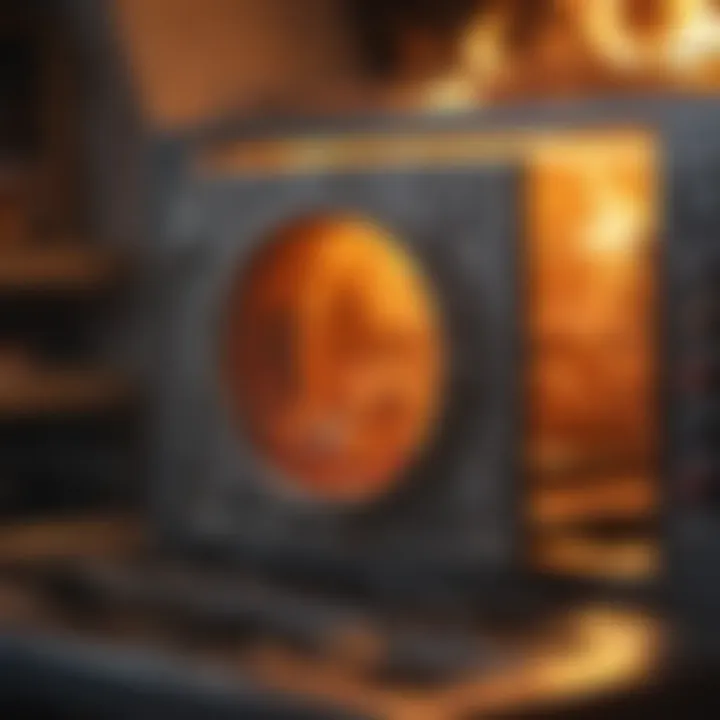
Factors to Consider When Choosing a Burnout Oven
When delving deep into the world of jewelry making, selecting the right burnout oven becomes a critical decision that can significantly influence the quality of the final product. The importance of choosing the appropriate burnout oven lies in its direct impact on the casting process in jewelry fabrication. Factors such as temperature range, consistency, size, capacity, and control features play pivotal roles in determining the efficiency and accuracy of the casting process. Understanding and carefully considering these factors can lead to enhanced precision, reduced defects, and overall improved quality in jewelry production.
Temperature Range and Consistency
Critical Parameters for Quality Casting
In the realm of jewelry fabrication, the temperature range and consistency of a burnout oven are paramount for achieving exceptional casting results. Maintaining precise temperature control throughout the burnout process is crucial to ensure the proper phase transitions of the materials being used. This critical parameter not only guarantees the successful completion of the burnout phase but also influences the final quality and integrity of the cast jewelry pieces. The ability to control and monitor the temperature with high accuracy is a key characteristic of top-tier burnout ovens, making them a preferred choice for artisans and designers aiming for excellence in their craft. The unique feature of precise temperature regulation in quality casting not only enhances the efficiency of the casting process but also minimizes the risk of defects, ensuring a superior end product in the realm of jewelry making.
Size and Capacity
Matching Oven Size to Production Needs
In the optimization of jewelry making processes, one must carefully consider the size and capacity of the chosen burnout oven to align with specific production requirements. Matching the oven size to production needs directly impacts the casting volume and efficiency of the overall jewelry fabrication workflow. An appropriately sized oven allows for optimal utilization of space and resources, ensuring that production output meets demand without unnecessary limitations. The key characteristic of matching oven size to production needs lies in its ability to streamline operations and enhance production scalability. Through careful consideration and alignment of oven size with production demands, jewelry designers and manufacturers can achieve a seamless workflow that maximizes output while maintaining quality standards.
Control Features and Programmability
Automation for Precise Results
The integration of advanced control features and programmability in burnout ovens revolutionizes the jewelry making process by offering automation for precise results. Automation plays a crucial role in enhancing the efficiency and accuracy of the burnout phase, allowing for consistent and repeatable casting outcomes. The key characteristic of automation for precise results lies in its ability to eliminate human error, resulting in a higher level of consistency and quality in the final jewelry pieces. The unique feature of programmable settings and automation not only streamlines the casting process but also empowers artisans and designers with the flexibility to experiment and innovate with different casting techniques. Overall, the incorporation of automation in burnout ovens ensures precise results, optimal performance, and improved productivity in the realm of jewelry fabrication.
Best Practices for Operating a Burnout Oven
In the realm of jewelry making, the segment dedicated to the Best Practices for Operating a Burnout Oven is a cornerstone of efficiency and precision. Understanding the intricacies of this practice is paramount for achieving top-notch results in jewelry fabrication. Employing the right techniques and approaches can significantly enhance the casting process, leading to impeccable outcomes that satisfy the demands of even the most discerning collectors and designers. By following these best practices, artisans can elevate their craft to new heights, ensuring that each piece created is a masterpiece of precision and detail.
Preparation and Loading Procedures
Cleaning and Preheating Steps
When delving into the realm of Cleaning and Preheating Steps within the context of operating a burnout oven, one must pay meticulous attention to detail. These initial steps lay the foundation for a successful casting process, ensuring that the jewelry pieces are free from any impurities that could compromise the final product. Cleaning and preheating not only aid in preventing defects but also contribute to the overall efficiency of the burnout process. Proper cleansing of the jewelry pieces followed by precise preheating sets the stage for flawless casting, enabling artisans to achieve the desired level of detail and quality in their creations.
Optimal Placement of Jewelry Pieces
Optimal Placement of Jewelry Pieces plays a crucial role in the casting process, determining the outcome of the final piece. The strategic arrangement of jewelry pieces within the burnout oven is instrumental in ensuring even heating and proper airflow, vital components for successful casting. By placing the pieces thoughtfully and optimally, artisans can mitigate the risk of thermal irregularities and achieve uniform results across all components. This meticulous approach not only enhances the efficiency of the burnout process but also contributes to the overall quality and precision of the final jewelry pieces. Attention to detail in the placement of jewelry pieces is key to mastering the art of burnout ovens and producing exceptional pieces consistently.
Monitoring and Controlling the Burnout Process
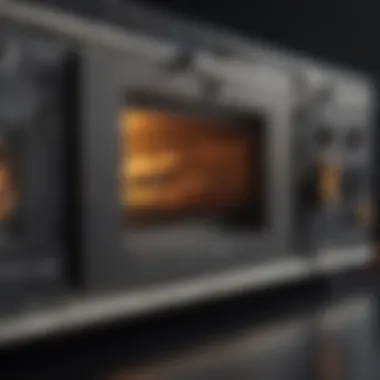
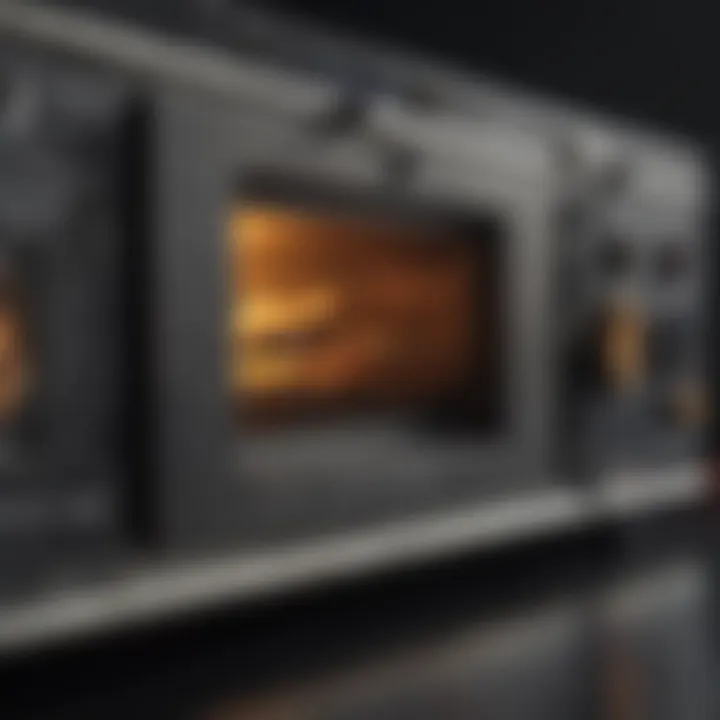
Temperature Regulation
A critical aspect of operating a burnout oven is Temperature Regulation, which directly impacts the casting outcome. Maintaining precise temperatures throughout the burnout process is essential for achieving the desired results, as variations can lead to defects or inconsistencies in the final product. Temperature regulation technology ensures that the burnout process proceeds smoothly, providing artisans with the control needed to produce high-quality jewelry pieces consistently. By leveraging temperature regulation effectively, artisans can optimize their casting process and achieve impeccable results that meet the highest standards of craftsmanship.
Timely Removal of Residues
Timely Removal of Residues is a key step in the burnout process that requires attention to detail and precision. Residues left behind during the burnout phase can impact the quality of the final casting, potentially leading to defects or imperfections. By promptly removing residues at the appropriate stages of the process, artisans can safeguard the integrity of their work and ensure that the final jewelry pieces meet the expected quality standards. Timely removal of residues not only enhances the aesthetics of the jewelry but also contributes to its overall durability and longevity, marking a crucial step in the path to excellence.
Cooling and Unloading Protocols
Post-Casting Handling for Quality Preservation
Post-Casting Handling for Quality Preservation is a critical stage in the burnout process that determines the longevity and integrity of the final jewelry pieces. Proper handling and cooling techniques post-casting are essential for preserving the quality of the pieces and safeguarding them from structural deformities or damage. The meticulous approach to cooling and unloading ensures that the jewelry pieces retain their intricate details and structural integrity, ready to be further processed or finished as per the artisan's design. By implementing the appropriate post-casting handling protocols, artisans can uphold the quality of their work and deliver pieces that captivate enthusiasts and collectors alike.
Maintenance and Troubleshooting Tips
The section on Maintenance and Troubleshooting Tips in this comprehensive guide on Optimizing Jewelry Making focuses on the critical aspects that ensure the smooth operation of burnout ovens. Delving into the intricacies of maintaining and troubleshooting these essential tools, this segment aims to provide gemstone enthusiasts, collectors, and jewelry designers with valuable insights into prolonging the lifespan and maximizing the efficiency of their equipment. Understanding how to effectively clean and calibrate burnout ovens is pivotal in ensuring consistent performance and high-quality jewelry fabrication.
Cleaning and Calibration
Regular Maintenance Practices
Regular Maintenance Practices hold a central role in the upkeep of burnout ovens, contributing significantly to the overall functionality and longevity of these devices. By establishing a routine maintenance schedule encompassing cleaning, inspection, and minor repairs, jewelry makers can prevent unforeseen breakdowns and maintain optimal performance levels. The key characteristic of Regular Maintenance Practices lies in their proactive approach to equipment care, preemptively addressing potential issues before they escalate. This methodical upkeep ensures a reliable and efficient workflow, safeguarding against costly repairs and delays in production. An advantage of Regular Maintenance Practices is their ability to enhance the durability of burnout ovens, enabling consistent performance over an extended period.
Ensuring Consistent Performance
Ensuring Consistent Performance is paramount in the realm of jewelry making, particularly concerning burnout ovens. By focusing on the consistent delivery of temperature control, airflow regulation, and operational accuracy, this facet plays a crucial role in achieving precise casting results. The key characteristic of Ensuring Consistent Performance revolves around the meticulous calibration and adjustment of oven settings to align with specific casting requirements. This meticulous attention to detail guarantees that each jewelry piece undergoes the casting process under optimal conditions, resulting in uniform quality and minimal defects. An advantage of Ensuring Consistent Performance is its ability to uphold the integrity of the casting process, promoting reliability and repeatability in jewelry fabrication.
Common Issues and Solutions
Identifying Malfunctions
Identifying Malfunctions is a foundational step in troubleshooting burnout ovens, essential for maintaining operational efficiency and productivity in jewelry making. By adeptly recognizing signs of malfunction such as temperature fluctuations, irregular noises, or inconsistent heating patterns, users can promptly address underlying issues before they impact casting quality. The key characteristic of identifying Malfunctions involves astute observation and diagnostic skills to pinpoint potential sources of errors within the oven system. This proactive approach enables swift remediation, minimizing downtime and ensuring uninterrupted workflow. A benefit of Identifying Malfunctions is its role in preemptively averting major breakdowns, thereby safeguarding against costly repairs and prolonged equipment downtime.
Troubleshooting Techniques
Troubleshooting Techniques form the cornerstone of effective oven maintenance and operational optimization in jewelry making. By employing systematic approaches to isolate and resolve issues such as heating irregularities, sensor malfunctions, or power supply disruptions, users can restore oven functionality efficiently. The key characteristic of Troubleshooting Techniques lies in their emphasis on methodical problem-solving methodologies, which involve logical deduction and systematic testing to identify and rectify faults. This strategic troubleshooting process allows for swift resolution of issues, enabling users to resume jewelry fabrication with minimal interruption. An advantage of Troubleshooting Techniques is their capacity to enhance user proficiency, fostering a deeper understanding of burnout oven mechanics and troubleshooting strategies.
Conclusion
In concluding the comprehensive guide on optimizing jewelry making through the utilization of burnout ovens, it is imperative to underscore the transformative impact that this technology has had on the craft. The realm of jewelry fabrication has experienced a significant evolution, with burnout ovens playing a pivotal role in enhancing efficiency, precision, and the overall quality of final products. By embracing the artistry of burnout ovens, artisans and designers are able to delve deeper into the intricacies of gemstone manipulation, catering to a discerning audience of gemstone enthusiasts, collectors, and jewelry designers.
Embracing the Artistry of Burnout Ovens
Within the fascinating world of jewelry making, the concept of embracing the artistry of burnout ovens emerges as a cornerstone of creativity and refinement. This approach epitomizes the fusion of technical expertise with artistic vision, allowing individuals to elevate their craft to new heights of excellence. By embracing the artistry of burnout ovens, practitioners can delve into the nuances of temperature control, material selection, and casting precision, thereby honing their skills and creating exquisite pieces that resonate with aficionados of fine jewelry. The ability to infuse each creation with a unique blend of artistry and technical mastery distinguishes true artisans in the field, captivating audiences with the allure of exceptional craftsmanship and innovative design.