Mastering Lapidary Saws and Polishers for Gemstone Art
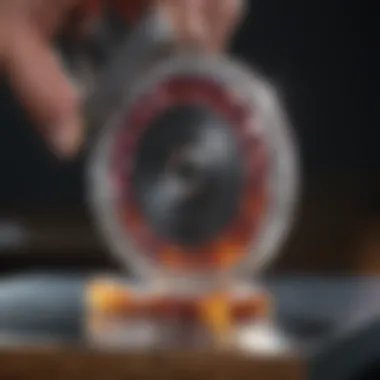
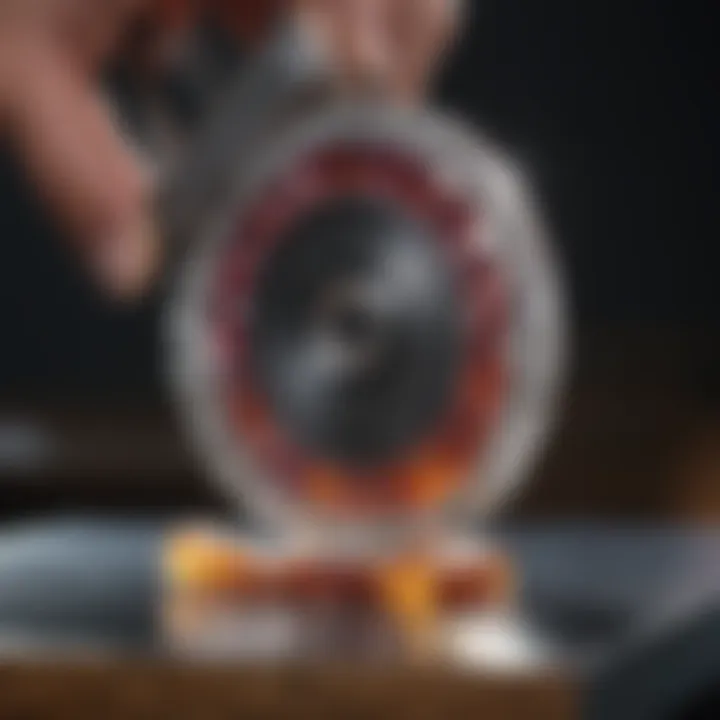
Foreword
Crafting beautiful gemstones and jewelry requires more than just raw materials. It involves a blend of art and science, where precision meets creativity. At the heart of this craft are lapidary saws and polishers. These tools play a pivotal role in turning uncut stones into exquisite pieces that dazzle the eye and capture the heart. Understanding how these tools work, along with the gemstones they shape, is crucial for anyone serious about this craft.
Gemstones, in their natural state, are often unrecognizable and lack the luster that captures our imagination. It’s through the lapidary process—sawing, shaping, and polishing—that their true beauty is revealed. This article dives deep into the tools of the trade, offering insights into the types of equipment available, their care and maintenance, and the techniques that ensure a quality finish.
Overview of Gemstones and Minerals
Understanding gemstones starts with grasping what makes them unique. They are not just pretty rocks; they possess geological complexities that influence their desirability and value. Here’s an exploration of their background.
History of Gemstone and Mineral Use
From ancient civilizations to modern society, gemstones and minerals have served various purposes. Historically, they were not only ornamental but also held significant status and power. Ancient Egyptians adorned themselves with lapis lazuli, believing it provided protection from evil, while the Greeks and Romans associated certain stones with the gods, enhancing their divine influence.
- Mining Traditions: Ancient cultures developed intricate mining techniques to extract gemstones, often using rudimentary yet effective tools.
- Trade and Value: Gemstones became commodities; their value often dictated by rarity and demand. The Silk Road, for example, facilitated the movement of precious stones between the East and West.
Significance in Culture and Society
Today, gemstones still hold cultural significance. They symbolize milestones such as engagements, births, and anniversaries. Different cultures have varying beliefs about gemstones. For instance, many believe that the right stone can bring luck or heal ailments. This deep-rooted connection shows that gemstones are more than just beautiful objects; they are woven into the fabric of human society.
"Through history, gemstones have bridged the gap between nature and humanity, imbuing the latter with beauty and significance."
Gemstone Formation and Properties
Understanding how a gemstone forms provides insight into its characteristics and the kind of tools needed for its crafting.
Formation Process of Gemstones
Gemstones originate from minerals, which form through geological processes over millions of years. These processes can include:
- Metamorphism: Heat and pressure cause minerals to change, creating beautiful stones such as garnet and ruby.
- Volcanic Activity: When magma cools, it can produce rare gems like obsidian or diamonds formed under high-pressure conditions deep within the Earth.
Properties that Define Gemstones
Several properties distinguish gemstones. Evaluating color, clarity, cut, and carat provides insights into a stone's quality:
- Color: The most visually apparent feature, influenced by light interaction and mineral composition.
- Clarity: Refers to the presence of internal or external flaws. A higher clarity rating typically increases value.
- Cut: How a gemstone is shaped and polished affects its brilliance.
- Carat: A measure of weight that helps define the value.
Classification based on Color, Hardness, and Luster
Gemstones can be classified into categories based on their properties. The Mohs scale is a common way to determine hardness:
- Hardness: Ranging from talc (1) to diamond (10), hardness is crucial for both identification and the practical use of the gemstone.
- Luster: This property describes how light interacts with the surface of the stone. It can be glossy, matte, or dull and adds to the stone's appeal.
Types of Gemstones
In the diverse world of lapidary, not all gemstones are created equal. They are broadly categorized as precious or semi-precious.
Precious vs. Semi-Precious Gemstones
Precious gemstones include:
- Diamond
- Ruby
- Sapphire
- Emerald
Semi-precious stones encompass a vast array of options, including:
- Amethyst
- Aquamarine
- Opal
- Turquoise
Common Gemstone Varieties
Some of the well-known varieties that you might encounter within the realm of gemstone and jewelry design include:
- Topaz: Often found in various hues, from pale blue to rich gold.
- Tourmaline: Renowned for its ability to exhibit multiple colors within a single crystal.
Exotic and Rare Gemstones
Beyond the commonly sought-after stones lie the rare, often elusive gems like:
- Alexandrite: Known for its color-changing properties.
- Painite: Once considered the rarest mineral on Earth, highly sought by collectors.
Understanding these exceptional gems can enhance not only appreciation but potential selection for your projects.
Identifying and Evaluating Gemstones
When entering the world of gemstones, knowing how to identify and evaluate them is crucial.
Factors Affecting Gemstone Value
Several factors influence the monetary and aesthetic value of gemstones. Key considerations are:
- Rarity: The less a gemstone is found in nature, the more valuable it typically becomes.
- Market Demand: Current trends can affect valuations significantly.
- Provenance: A gem's history and origin often increase its appeal.
Techniques for Gemstone Identification
Techniques for identifying gemstones can range from simple visual inspections to more complex methods involving technology:
- Magnification: Inspecting stones under magnification helps to identify inclusions or flaws.
- Refractive Index Testing: This scientific method allows lapidaries to determine whether a stone is natural or synthetic.
Assessing Gemstone Quality
Assessing quality involves scrutinizing the Four Cs: color, clarity, cut, and carat weight. Well-rounded knowledge of these aspects enhances overall evaluation and decision-making when purchasing or working with gemstones.
Caring for Gemstones
Proper care of gemstones is paramount to maintain their beauty and integrity.
Cleaning and Storing Gemstones Properly
Cleaning should be done with care—some gemstones require specific methods. For instance:
- Water and Mild Soap: Generally safe for many stones, while harsher chemicals can damage softer varieties.
- Storage: Storing in separate cloth pouches can prevent scratches and damage.
Avoiding Common Mistakes in Gemstone Care
Common mistakes often stem from a lack of knowledge. Avoid exposing gemstones to:
- Harsh Chemicals: Such as bleach or ammonia, which can cause irreparable damage.
- Extreme Temperatures: Sudden changes may lead to fractures or discoloration.
Preservation Tips for Specific Gem Types
Each gemstone has its own quirks. For example:
- Opals: Require moisture to maintain their beauty, making it vital not to let them dry out.
- Turquoise: Needs to be protected from oils and sweat, which can alter its appearance.
Collectively, these insights ensure a longer lifespan and sustained beauty for gems in your collection.
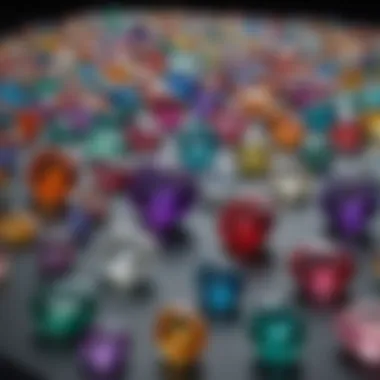
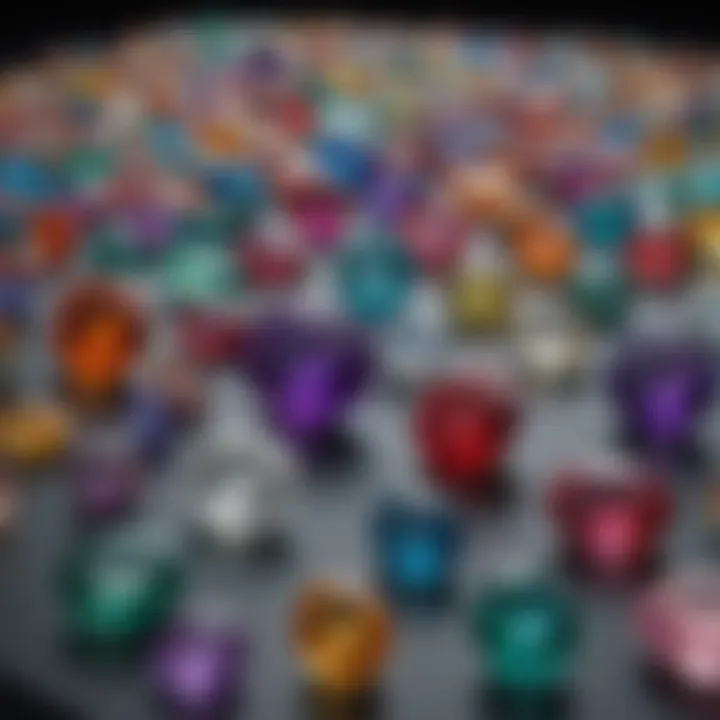
As we move forward, we’ll take a closer look at the lapidary saws and polishers that enable the transformation of these stunning stones, detailing functionalities, and maintenance to ease your journey into gem crafting.
Foreword to Lapidary Tools and Techniques
Lapidary work is more than just a craft; it’s a confluence of artistry and precision, requiring the right tools to transform raw stones into beautiful gems. This article delves deeply into lapidary saws and polishers, which are indispensable in the crafting of exquisite gemstone jewelry. Without effective tools, even the finest pieces of gemstone can remain unshaped and dull, lacking the brilliance they are meant to showcase.
When considering lapidary tools, one should recognize their role not only in the physical shaping of stones but also in the skill development of the artisan. Mastering these tools can greatly enhance one’s ability to create intricate and stunning designs. Moreover, using the right lapidary equipment can significantly improve efficiency. As tools evolve, so too do the techniques, opening new avenues for creativity and accuracy in gemstone processing.
Historical Context of Lapidary Arts
Lapidary has roots that stretch back centuries, originating from ancient civilizations that valued gemstones for both their beauty and believed mystical properties. The Egyptians, for instance, were adept at using rudimentary tools to shape stones like lapis lazuli and turquoise, often called upon for use in jewelry and ornamental items. This was an art form grounded in necessity, as well as aesthetics.
With the progression of time, different cultures began to develop their own lapidary techniques. The Romans advanced the art through the introduction of cutting wheels, while the Chinese were known for their precision in jade carving. Each era contributed unique methodologies and tools to the craft - laying the groundwork for modern lapidary practices. Thus, understanding this historical context is crucial for today’s enthusiasts, as it shapes the principles guiding the use of contemporary lapidary saws and polishers.
Importance of Lapidary Saws and Polishers
Lapidary saws and polishers stand as the backbone of gemstone crafting, facilitating the transition from raw material to refined artwork. These tools are not merely accessories; they represent a significant investment in both time and capital for artisans. Without them, the process of cutting and finishing gemstones would be laborious and potentially detrimental to the stones themselves.
- Precision Cutting: Saws allow for accurate cuts that can be tailored to the specific hardness and composition of each stone, preserving its integrity and maximizing aesthetic appeal.
- Finishing Touches: Polishers are essential for achieving the luster that elevates a stone from ordinary to extraordinary. The final polish is often what reveals the true beauty of a gemstone, enhancing its color and depth.
- Efficiency: Advanced lapidary equipment can save time and improve craftsmanship by reducing manual labor. Technological advancements mean that many saws and polishers are now designed to minimize waste and to work with greater accuracy.
A skilled lapidarist doesn’t just cut stone; they unearth the inherent beauty lying dormant within.
In summary, lapidary saws and polishers play an integral role in the jewelry making process, marrying the scientific principles of material properties with the art of design. By comprehending their importance, gemstone enthusiasts can fully appreciate the profound skills involved in the mesmerizing world of lapidary arts.
Understanding Lapidary Saws
Lapidary saws play a pivotal role in the precision cutting and shaping of gemstones. They are the unsung heroes in the lapidary process, ensuring that raw stones are transformed into beautifully crafted pieces ready for polishing and setting in jewelry. The selection of an appropriate saw can make or break a project, affecting not only the outcome but also the efficiency of the work. Thus, it's important to delve into the specifics of lapidary saws to appreciate their significance fully.
Types of Lapidary Saws
Lapidary saws come in various types, each tailored to specific cutting tasks. Understanding these variations is crucial for achieving the desired results.
Diamond Saws
Diamond saws are often seen as the gold standard for lapidary work. The key characteristic of these saws is their blades embedded with diamond particles, which allows them to slice through even the hardest materials, such as quartz and sapphire. Their efficiency cuts down on time, making them a popular choice among professionals and hobbyists alike.
The unique feature of diamond saws is their durability; they can last far longer than traditional blades under similar use. However, they come at a higher price point, which might deter beginners on a budget.
Circular Saws
Circular saws are versatile tools that can be used for a variety of cutting tasks. They are characterized by their rotating blades, which make quick work of thin slices. This is particularly beneficial when working with brittle materials, as you can achieve precise cuts without much risk of fracturing the stone.
In terms of advantages, circular saws are highly effective for slicing larger rocks into manageable pieces. Though efficient, they can cause more dust and debris compared to other types, potentially requiring more cleanup.
Slab Saws
When it comes to cutting thicker materials, slab saws shine. These saws employ a wide blade that is capable of slicing through sizable stones, yielding large slabs. Because of their capability, they are especially favored for gem enthusiasts looking to make exclusive cuts from large specimens.
A unique aspect of slab saws is their ability to provide uniform thickness in the cuts, ensuring consistency, which is important for quality craftsmanship. However, they require a sturdy setup and can take up considerable workspace.
Wire Saws
Wire saws offer a different approach with their thin, flexible blades that resemble a wire with diamond grit. They are particularly useful for intricate cuts and delicate materials. The flexibility of wire saws means they can navigate curves and corners more easily than rigid blades, making them ideal for detailed work.
Nevertheless, one must be gentle when using wire saws, as applying too much pressure can lead to breakage. They also require more time for cutting compared to their more robust counterparts.
Components of a Lapidary Saw
Understanding the components of a lapidary saw goes hand in hand with utilizing it effectively. The makeup of these tools is what enables them to function optimally and suits different user needs.
Blade Types and Materials
Blades vary significantly in lapidary saws, with materials ranging from steel to composite varieties. The most common blade type utilized is the diamond blade, known for its exceptional cutting abilities. The primary advantage is its capacity for cutting a diverse range of materials without much wear.
However, not all cuts require diamond; steel blades can work well for softer stones. The choice really depends on the intended application and desired precision.
Motor and Power Specifications
The motor of a lapidary saw is possibly the most critical component. It defines the power and speed at which the saw operates. Depending on the motor specifications, various cutting speeds can be achieved. A powerful motor is essential for cutting through tough materials, whereas a less powerful motor might struggle, leading to overheating or even failure during operation.
Choosing a motor that fits your expected workload and stone type is beneficial, allowing for smoother operation and longevity.
Water/Cooling Systems
A saw's cooling mechanism is vital to the cutting process, especially for long sessions. Water cooling systems reduce heat buildup, prolonging the life of the blade and enhancing cutting accuracy. The primary characteristic of these systems is their integration into the saw’s design, allowing for a steady stream of water to flow over the blade.
Despite their importance, not all lapidary saws come equipped with cooling systems, which is something to consider if you’re planning to work on tougher materials for extended periods.
Choosing the Right Lapidary Saw
Selecting the right lapidary saw requires thoughtful consideration of various factors unique to the user’s needs. Having the ideal saw can improve outcomes and streamline processes.
Assessing Material Types
Before diving in, it’s essential to assess the types of materials you plan to cut. Varying stone hardness can dictate the type of saw and blade needed. Understanding whether you're dealing with soft stones like calcite or harder ones such as jade will significantly influence your choice.
Budget Considerations
Budget is often a decisive factor in tool selection. While it's tempting to invest in the top-tier diamond saws, there are many cost-effective options that perform admirably for less demanding projects. Striking a balance between quality and affordability can yield considerable savings while still meeting your lapidary needs.
Space and Portability Needs
The workspace available will greatly affect your selection. Some saws, like slab saws, can occupy a hefty footprint, requiring more real estate to operate effectively. If you're limited in space, a more compact option may be necessary, perhaps leaning towards smaller circular or diamond saws. Additionally, if you intend to move around regularly, consider the portability feature, as heavier saws can become cumbersome.
The Process of Using a Lapidary Saw
Using a lapidary saw is a fundamental process in the art of shaping and preparing gemstones. Understanding the intricacies of this procedure not only enhances the quality of the finished product, but also ensures efficiency and safety throughout the process. From selecting the right stone to the precision of the cut, every element contributes significantly to the craftsmanship that lapidary enthusiasts and professionals alike strive to achieve.
Preparing the Gemstone
Selecting the Right Stone
Selecting the right stone is the first step in successful lapidary work. Each gemstone comes with its characteristics, which can greatly influence the cutting process. For example, softer stones like calcite can be easily worked with, making them ideal for beginners. In contrast, more resilient stones, such as sapphires, require advanced techniques and equipment.
The key aspect of this selection is understanding the hardness and grain of the stone, which dictates how well it can withstand cutting and polishing. If you choose an unsuitable stone, like a fractured quartz, your efforts might go to waste in the long run. This careful selection is an investment into the quality of your work and can save time and resources.
Marking Cuts and Measurements
Marking cuts and measurements is another critical stage in the sawing process. Without accurate guidelines, one risks wasting material or damaging the stone. Properly marking the gemstone not only sets the stage for clean cuts but also ensures consistency throughout the lapidary process. Experienced lapidarians often use specialized tools for this, such as pencils or markers suited for pedras, as they leave minimal residue.
One effective technique involves taking careful measurements using calipers to determine where cuts should occur, providing both precision and confidence when making the first cut. This forms the foundation upon which all further work depends, making it a popular practice in both amateur and professional laps.
Executing the Cut
Cutting Techniques and Tips
Executing the cut effectively is at the heart of lapidary crafting. A key technique is to let the saw do the work, allowing the blade’s sharpness and the right feed rate to dictate the cutting speed. Engaging in rhythm rather than applying excessive pressure helps avoid chipping or fracturing the stone.
Another noteworthy method involves making a pilot cut or starting at the edge of the stone–it prevents slipping and allows for more control. This technique not only fosters smoother cuts but also extends the life of the blade itself.
Safety Precautions
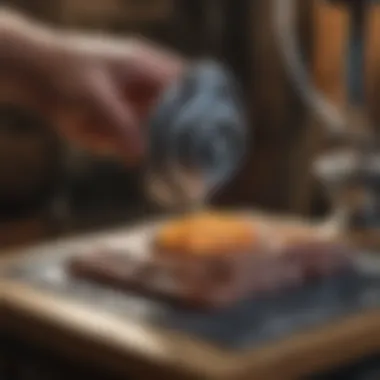
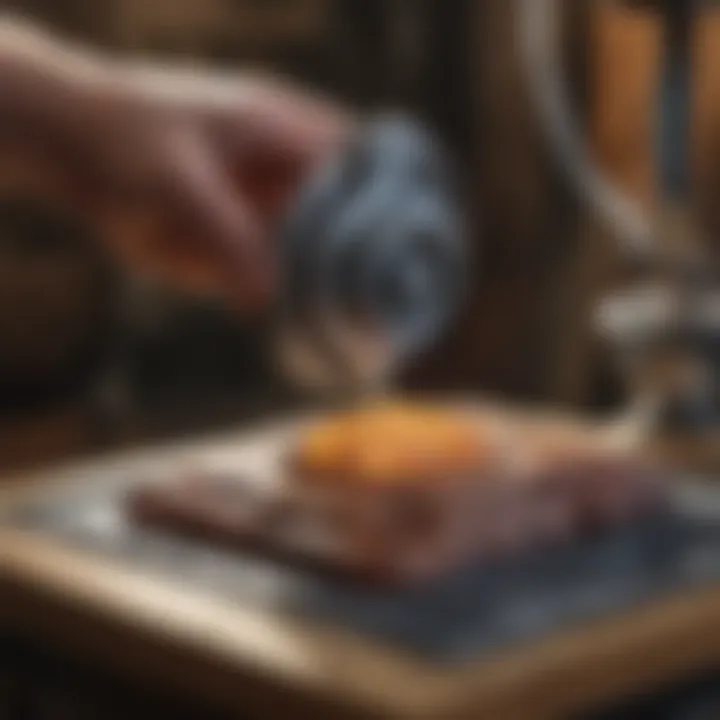
Safety precautions are paramount in any lapidary work. Wearing proper personal protective equipment, such as safety goggles and gloves, reduces the risk of injury from flying debris or sharp edges. Moreover, ensuring the workspace is clear of clutter and that all equipment is in good condition is crucial for maintaining safety while working.
One unique feature of lapidary saws is the use of water as a coolant and dust suppressor. Keeping the stone wet minimizes the chances of overheating the blade, which can lead to costly damages to both the equipment and the stone. Therefore, understanding and implementing these safety measures not only protects the user but also enhances the efficiency of the work.
Post-Cutting Procedures
Cleaning the Cut Surface
Cleaning the cut surface may seem trivial, but it plays a significant role in the next stages of lapidary work. After cutting, residues and residue dust must be removed to prevent contamination during polishing. Using a soft brush and warm water is often a recommended method. For stubborn residues, a gentle soap solution can help break them down.
The advantage of this cleaning is twofold; not only does it prepare the surface for polishing, but it also allows for a thorough inspection of the cut quality without any hindrances from leftover materials.
Inspecting for Flaws
Inspecting for flaws after cutting is essential to identify any defects that may hinder the polishing process or compromise the overall quality of the finished gemstone. A jeweler's loupe or a magnifying glass is commonly used for this purpose. Detecting issues early allows for effective corrections or adjustments.
The unique insight gained from examining the stone significantly contributes to the creation of a aesthetically pleasing final product. While it might take extra time, this step is often viewed as a beneficial practice, even by seasoned artisans.
Proper preparation and post-cutting checks are not just best practices; they are the difference between a good lapidary job and a truly exceptional one.
Exploring Lapidary Polishers
Lapidary polishers play a vital role in transforming rough gemstones into stunning pieces of art. They’re like the final brush strokes on a canvas, bringing out the beauty that lies beneath the surface. In the realm of gemstone crafting, the quest for a perfect shine is nearly an art form itself, merging craft and precision. Polishers are essential for achieving that smooth finish that collectors and designers alike covet, enabling gems to spark joy when held up to the light.
With the right polishing equipment, lapidaries can achieve various finishes, from a high gloss to a matte look, depending on the desired outcome. It’s all about choosing tools that best serve your specific goals. Let's explore the different types of polishers available, how they work, and what to consider when selecting one for your lapidary projects.
Types of Lapidary Polishers
Tumbling Polishers
Tumbling polishers are popular among hobbyists for their simplicity and effectiveness. They provide a continuous motion solution that allows multiple stones to be polished together, which is particularly useful for smaller gems or beads. A key characteristic of tumblers is their ability to smooth out stones uniformly. This means that even a mix of different stones can come out looking like a polished collection, which is a notable boon for those just starting out.
One unique feature of tumbling polishers is the rotating barrel where stones and polishing compounds mix. The advantages of this type include low cost and ease of use, making them a solid choice for beginners. However, they can be time-consuming, often requiring days to achieve the desired polish.
Flat Surface Polishers
Flat surface polishers offer a different approach, focusing on flat items or slabs of stone. Their main benefit lies in their precision; they are particularly useful for artists looking to create flat surfaces on their gemstones. These polishers can yield high-quality results quickly, making them favorable for more experienced artisans.
What sets flat surface polishers apart is their flat disc design, allowing for even pressure distribution during polishing. Their main downside, however, is limited compatibility with irregularly shaped stones, making them less versatile than tumbling options. Choosing flat surface polishers can lead to exceptional polish on slabs, however, it may restrict creativity if your work involves a range of shapes.
Spindle Polishers
Spindle polishers are specialized tools designed for achieving intricate details on gemstones. They allow for precision work on various shapes and sizes with the use of different attachments for polishing. This makes them particularly favorable for jewelry designers who need to work on detailed designs. Their adaptability to a wide range of tasks is a notable advantage, as you can customize polishing from fine to coarse finishes with the right heads.
One unique feature of spindle polishers is the adjustable RPM, which allows users to control the polishing speed, aiding in avoiding over-polishing. However, this equipment often requires a higher level of skill and understanding, making it less ideal for novices. That said, for those willing to invest time in learning, spindle polishers can yield striking finishes that set designs apart.
Key Components of Polishers
Polishing Pads and Compounds
Polishing pads and compounds are fundamental to the success of any lapidary polisher. A great pad can mean the difference between a mediocre finish and a breathtaking shine. These pads come in various materials and textures, allowing users to select the right ones based on the stone type and desired finish.
For instance, softer pads are generally used for delicate stones while harder pads provide deeper polishing effects on tougher materials. The choice of compound is essential, as it not only affects the final appearance but also the safety of the gem being polished. It’s crucial to choose wisely, as some compounds can be too abrasive for softer stones, leading to lasting damage.
Drive Mechanisms
Drive mechanisms are what power polishers, determining how efficiently they operate. Different mechanisms can be more effective for certain tasks or polishing speeds. In general, electric motors are the most common, offering reliability and consistent power.
The unique feature here is the mechanism’s ability to maintain torque even under load, ensuring the polishing doesn’t slow down when pressure is applied. However, if the motor isn't sufficiently powerful, there can be delays in polishing effectiveness and potential overheating, which is a detriment in the long run.
Speed Control Features
Speed control is immensely critical in polishing; the correct RPM ensures your stones are treated with care. Having control over the speed helps in adapting to various stone types and desired finishes, which makes it a crucial feature for any serious lapidary. Higher speeds can achieve quicker results but may risk damaging more delicate stones.
The appealing aspect of speed control is the ability to fine-tune the polishing process depending on the needs of the particular piece. On the downside, these features can sometimes be prone to malfunctions if the machinery isn't maintained properly, which might lead to inconsistent outcomes.
Selecting the Appropriate Polisher
Material Compatibility
Material compatibility is a significant factor to consider when selecting a lapidary polisher. A well-suited polisher will be able to handle the specific types of stones you plan to work with, whether they are soft marbles or harder jades. This is essential because a mismatch can lead to ineffective polishing or potential damage to the stone.
The standout aspect of checking compatibility lies in understanding the stones you're working with, leading to more efficient polishing sessions. On the downside, becoming overly reliant on a polisher due to its compatibility can limit exploration of other stones.
Desired Finish Quality
Different projects demand various levels of polish, from a glossy shine to a satin finish. Understanding what kind of finish you want will inform the selection of your polisher. Some polishers excel at high gloss finishes, while others are better for achieving a more subdued appearance.
One unique characteristic is the effect of compound and pad selection on the finish. High-quality pads combined with the right polishing compounds can elevate the final product dramatically but may require more investment. Conversely, opting for low-cost solutions might cut down quality, so it’s a classic case of balancing cost versus quality.
Operator Experience Levels
A polisher's efficiency often correlates directly with the user’s experience level. Beginners may find more straightforward tools beneficial, while seasoned lapidaries might prefer features that allow for greater customization. Depending on your experience, certain polishers could either simplify the process or complicate it.
The unique advantage of considering operator experience is that it allows for the growth of skills and capabilities over time. However, starting with too complex of an equipment can be discouraging for newcomers, leading them to abandon the craft altogether.
Techniques for Effective Polishing
Polishing is the finishing touch that brings gemstones to life. It's not merely about shining a rock; it's about enhancing its innate beauty and ensuring that the meticulous work done prior truly stands out. Techniques for effective polishing require an understanding of both the tools at your disposal and the characteristics of the stones you are working with. In this section, we'll explore different elements of polishing, such as selecting the right compound, recognizing proper surface preparation, exploring methods for achieving a crisp finish, and evaluating that final polish—all critical steps in the lapidary process.
Preparing to Polish
Choosing the Right Polishing Compound
Choosing the right polishing compound is paramount. Each compound serves a distinct purpose, depending on the mineral composition of the gemstone. For instance, aluminum oxide is favored for its versatility with softer stones, while cerium oxide is often preferred for quartz due to its fine finishing capability. The primary characteristic that makes cerium oxide stand out is its ability to produce a high luster with minimal scratches.
Moreover, the type of gemstone impacts the choice of compound. Some compounds work wonders with specific minerals but may not fare well with others. This targeted approach is a significant advantage in achieving the desired sheen on your gemstones. However, it’s essential to factor in the potential mess that various compounds can cause during application, as some can create dust that necessitates proper ventilation and cleanup afterward.
Understanding Surface Preparation
Surface preparation sets the stage for effective polishing. This step ensures that the surface is free from scratches, pits, and other imperfections that could mar the final finish. A key characteristic of this step is using progressively finer grits of sandpaper or diamond pads, making sure each layer is smoothed out before moving on to the next. By investing time into this initial process, you create a solid foundation for a stunning finish.
A unique feature of surface preparation is its impact on the polishing time itself. A meticulously prepared surface often translates into less time spent on actual polishing. However, it's a balancing act; in a rush to finish, skipping this preparatory stage can lead to mediocre outcomes that do not meet the standards expected in gem crafting. Thus, patience is a virtue in the world of lapidary work.
Polishing Methods
Slow and Steady Approach
The saying "slow and steady wins the race" rings true in polishing, where rushing can lead to diminished results. This approach emphasizes taking your time to ensure every corner and facet receives adequate attention. The key characteristic of this method is its capacity to prevent overheating and unwanted scratches. This might not seem like much, but overheating can result in distortion or even cracking in certain gems, a costly mistake for any lapidary enthusiast.
One downside, however, is that this method can be time-consuming, especially if you’re working with more extensive batches. But considering the results—a shimmering finish unmarred by errors—it’s often worth the wait for the polished gem.
Using Polishing Patterns and Motions
Applying specific polishing patterns and motions can drastically improve the efficiency of the polish while ensuring an even distribution of the compound across the stone. Creating a systematic approach, often circular or figure-eight motions, allows for a consistent application of pressure and compound throughout the surface.
One key feature of this technique is that it maximizes contact with the polishing medium, enhancing the overall finish. Yet, this method requires some practice to perfect. Inconsistent application can lead to some areas being overly polished while others may remain dull. It’s a fine line, but once mastered, it can lead to stellar results in gemstone crafting.
Evaluating the Finish
Assessing Luster and Clarity
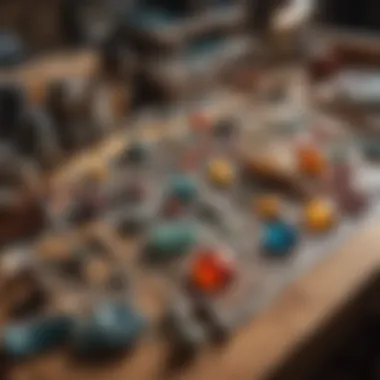
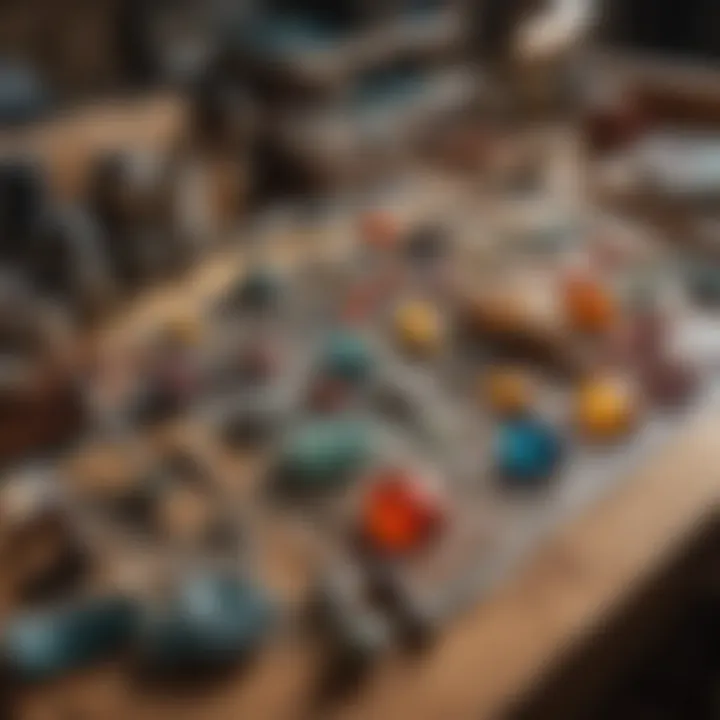
After applying the polish, assessing luster and clarity becomes the next crucial step. Luster refers to the way light interacts with the gemstone’s surface. A well-polished gem should reflect light brilliantly, appearing clear and inviting.
In evaluating this aspect, enthusiasts often rely on natural light to gauge the stone's brilliance. The unique feature here is the immediate feedback the gem provides when held against various lighting conditions. However, poor lighting or incorrect angles may cloud your evaluation, so patience in this step is critical to ensure accurate assessment.
Common Issues and Solutions
Despite meticulous polishing efforts, issues such as haziness, scratches, or uneven surfaces might arise. Identifying these common problems is crucial. For instance, haziness can often be attributed to insufficient polishing time or an inappropriate compound used for the material.
One effective solution entails going back a step and re-evaluating the surface preparation or switching to a finer compound for the finishing touches. Often, simply taking a moment to troubleshoot can save an invaluable piece from becoming a frustrated memory. By understanding these common pitfalls and their solutions, a lapidary can effectively refine their craft and achieve consistent results in their gemstone creations.
"In the world of lapidary arts, attention to detail is what transforms raw stone into a masterpiece. Every step counts."
In summary, the practices surrounding effective polishing are far from one-dimensional. Individual techniques are interconnected and require discernment and adjustment based on unique circumstances. Building these skills takes both practice and patience, but the results—gems that sparkle with clarity and elegance—are undoubtedly worth the effort.
Maintaining Lapidary Equipment
Maintaining lapidary equipment is not just a matter of keeping the tools shiny and operational; it’s about ensuring the longevity and effectiveness of your lapidary saws and polishers. Regular upkeep can elevate the quality of your work and enhance the efficiency of your processes. When your tools are in top shape, they can deliver smoother cuts and better finishes, which is essential for creating gemstones and jewelry that stand out.
Routine Maintenance Practices
Cleaning Procedures
Cleaning procedures form the bedrock of effective equipment maintenance. Regularly wiping down saws and polishers keeps residue from building up, which can lead to overheating and poor performance. A dirty cutter blade, for instance, can cause inconsistencies in cuts. The key characteristic of cleaning is that it’s often straightforward and doesn’t require advanced skills but reaps considerable benefits.
The unique feature of proper cleaning is using appropriate solvents and brushes that won't damage the equipment. For instance, using water with a mild detergent can be a popular choice, as it effectively removes dust and oils without causing harm. Just like brushing your teeth, if you neglect this step, you’ll face bigger problems down the line: uneven cuts and a higher risk of equipment failure.
Inspection and Part Replacement
Inspection and part replacement go hand-in-hand with cleaning. Checking your equipment for wear and tear can save you from costly repairs or replacements later on. This practice involves looking for worn-out blades, loose screws, or damaged components. When you routinely inspect your tools, you can often identify problems before they spiral out of control.
What makes inspection beneficial is that you can spot minor issues before they become major headaches. For example, a small crack in a blade could cause severe vibrations or dangerous failures if left unchecked. The unique aspect of this routine is that it not only prolongs the lifespan of your tools but also optimizes their performance — ensuring every gem comes out looking its best.
Safety and Storage Considerations
Saw and Polisher Storage Solutions
How you store your lapidary equipment can greatly affect its condition. Storing saws and polishers in a dry, secure place protects them from moisture and accidents. An effective storage solution might be a simple toolbox or dedicated cabinet where tools are safely tucked away.
The primary characteristic of good storage is accessibility; you shouldn’t have to dig through piles of clutter just to find your favorite saw. Based on the unique needs of the tools, specialized racks can be a beneficial choice, allowing equipment to be stored vertically, which conserves space and minimizes damage. However, one should remember that with such specialized storage, it’s crucial to keep the area clean to prevent accidental scratches or damage.
Understanding Electrical Safety
Electrical safety is another paramount consideration when working with lapidary equipment. Many saws and polishers run on electricity, and improper handling could lead to serious accidents. Understanding the electrical specifications of your tools—including how to manage overload situations—can help mitigate these risks.
A key characteristic of electrical safety measures is the use of properly grounded outlets. This may seem like a mundane detail, but not utilizing grounded sockets can lead to equipment being damaged or pose a risk of electric shock. The unique aspect of adhering to electrical safety protocols is that it ensures that both the operator and the equipment remain safe, saving you from potential mishaps in the workshop.
Troubleshooting Common Problems
Identifying Performance Issues
Identifying performance issues efficiently can save time and prevent mistakes that may ruin your work. When a saw doesn't cut smoothly or a polisher leaves scratches, the sooner you know, the better. Common issues may include blade dullness or improper alignment.
This practice is valuable because it prevents minor problems from transforming into significant failures. For example, loud vibrations during operation usually indicate a misalignment. The unique feature of effectively identifying issues is that systematically tracking tools' performance can lead to early interventions, ultimately enhancing the quality of your lapidary work.
Repairing or Replacing Parts
Repairing or replacing parts gives life to your lapidary tools. Understanding when a part needs to be repaired versus when it simply needs replacement can prevent further damage to the equipment. Regular maintenance can help you determine if a minor adjustment will suffice or if it’s time for a replacement.
The characteristic that makes repairs beneficial is that they can often be done quickly and cost-effectively. Replacing an entire saw due to a small issue could be a financial misstep. Knowing the unique features of your tools, including part compatibility, helps make informed decisions. Failing to recognize the signs of wear can lead not only to poorly executed projects but may also necessitate a total replacement of equipment, which should be avoided whenever possible.
Emerging Technologies in Lapidary Practices
The world of lapidary arts is not standing still; it is flourishing with innovation, making significant strides to enhance both efficiency and quality. Emerging technologies in this realm do not merely represent a trend but signify a pivotal evolution in lapidary practices. These advancements provide gemstone enthusiasts and professionals with tools that can drastically improve precision, reduce material waste, and even offer environmentally friendly alternatives. From computerized machining to the development of new materials, the future of lapidary is brighter than ever.
Computer Numerical Control (CNC) in Lapidary
Precision and Customization
One of the standout features of CNC technology in lapidary practice is its precision and customization. With CNC machines, artisans can execute designs with millimeter accuracy. This high level of precision translates into less wasted material and more refined final products. For instance, if a lapidary artist is crafting intricate inlays, CNC machining can replicate the designs exactly, making it a sought-after choice among professional gem cutters.
Additionally, customization is seamless with CNC technology. Users can input specific dimensions and designs directly into the system, allowing for unique creations that would be incredibly tedious to achieve by hand. The unique feature here is the software integration that allows for complex programming, enabling artists to experiment with various shapes and facets.
However, the disadvantage lies in the steep learning curve involved and the initial costs of acquiring such machines. Nevertheless, the long-term benefits of saving time and resources often outweigh these initial hurdles.
Integration into Traditional Practices
Despite the technological advancements, integration into traditional practices remains crucial. Many artisans still cherish the hands-on methods and the artistry that comes with them. The key characteristic of Integration into Traditional Practices is how CNC can complement rather than replace traditional handcrafting.
For instance, a lapidary might choose to use a CNC band saw for the rough cut and then finish the detailing by hand. This blended approach maintains the personal touch many artisans seek while benefiting from the precision that modern technology offers. The unique feature here is the ability to enhance creativity through additional tools. By merging old-world craftsmanship with cutting-edge technology, lapidary work can cover a wider spectrum of designs.
However, one of the downsides could be the loss of some traditional skills if over-reliance on CNC machinery occurs. Hence, finding a balance is essential for maintaining the integrity of the craft while embracing innovation.
Innovative Materials for Saw Blades and Polishers
Advancements in Diamond Technology
The field of Advancements in Diamond Technology has seen a remarkable boost. Diamond blades used in lapidary saws are now more durable and cost-effective than ever. These innovations often involve the inclusion of synthetic diamonds, which present a myriad of benefits. The key characteristic of modern diamond technology is that these blades offer a significantly longer lifespan, allowing for extended periods of uninterrupted work.
Another unique feature is the variety of bonds that can be engineered into the blades, allowing for specific uses and material compatibility, from soft stones to an ultra-rigid diamond itself. This enables lapidaries to choose blades perfectly suited to their specific tasks. While these advancements represent a significant leap forward, the cost can be a barrier for hobbyists. Yet, those serious about their craft often see this as a worthwhile investment.
Eco-Friendly Polishing Solutions
On the other hand, the movement toward Eco-Friendly Polishing Solutions is gaining traction. With increasing awareness of environmental issues, many artisans are searching for alternatives to traditional polishing compounds that may contain harmful substances. The unique feature within this domain is the development of polishing compounds made from biodegradable materials. These eco-friendly options not only reduce environmental harm but also offer effective polishing results.
The noticeable advantage of eco-friendly solutions is the less toxic nature of the materials being used, which is safer for both the artisan and the environment. However, some users have reported that these alternatives may require longer polishing times compared to traditional chemicals, which could interfere with productivity. Nevertheless, for environmentally-conscious gem artisans, these solutions represent a positive shift in best practices.
"The integration of technology and eco-friendly practices in lapidary not only refines the craft but also marks a new era of responsible artistry."
Epilogue: Mastering the Art of Lapidary Work
As we draw the curtains on our comprehensive journey through the world of lapidary saws and polishers, it becomes clear that mastering these tools is not merely about technical prowess; it is an art rooted in tradition and science. So much of what we discussed highlights how essential these devices are in transforming raw rock into beautiful gemstones. The craftsmanship involved requires patience, skill, and, quite frankly, a fair bit of passion.
Reflection on Lapidary Skills Development
Embarking on the path of lapidary arts isn't a walk in the park. Initially, many might cringe at the thought of wielding a saw or a polisher for the first time. Yet the beauty of this craft is that it allows anyone with a bit of determination and creativity to hone their skills over time. Development in lapidary skills revolves around a trial-and-error mindset. It's about learning to listen—both to the material you are working with and to your own intuitive voice.
One should not underestimate the value of practice. The more stones you cut, the better your understanding of their unique characteristics. Generally, newcomers often find themselves taking small steps—maybe starting with softer stones, such as quartz, before attempting tougher materials like granite. Furthermore, attending workshops or participating in relevant online communities, like slight familiar groups on reddit.com, can open gateways of knowledge not easily found in books.
Here are some key considerations for skill enhancement:
- Daily Practice: Carve out time each day to refine your techniques.
- Engage with Experienced Lapidarists: They can offer tips you won’t find in manuals.
- Document Your Progress: Keeping a log of your projects helps visualize growth and identify areas for improvement.
The Future of Gemstone Craftsmanship
Looking ahead, the future of gemstone craftsmanship appears vibrant and filled with potential. Technological advancements are reshaping how we approach lapidary work. Innovations like computer-aided designs and advanced CNC machinery are making the process more efficient and precise, ensuring that every cut and polish is executed with a level of detail once thought unattainable.
Moreover, environmental concerns are pushing many artisans to seek eco-friendly practices. The lapidary community is increasingly interested in sustainable materials and methods that minimize waste and reduce the carbon footprint associated with gemstone processing. Adapting to these changes ensures respect for the environment and preservation of this ancient craft for future generations.
In the coming years, we may also see more hybrid methodologies blending traditional techniques with modern technologies. This evolution promises to create unique textures and finishes, opening up new avenues for artistic exploration.
In sum, the world of lapidary art is transforming, potentially speeding towards a future where creativity and craftsmanship innovate harmoniously. As you indulge in this artistic journey, take heart in knowing that, whether through cutting-edge technology or classic techniques, the richness of lapidary skills continues to grow—nurturing both the soul of the artisan and the beauty of the gems they create.